Ensuring Mechanical Integrity in New Parts
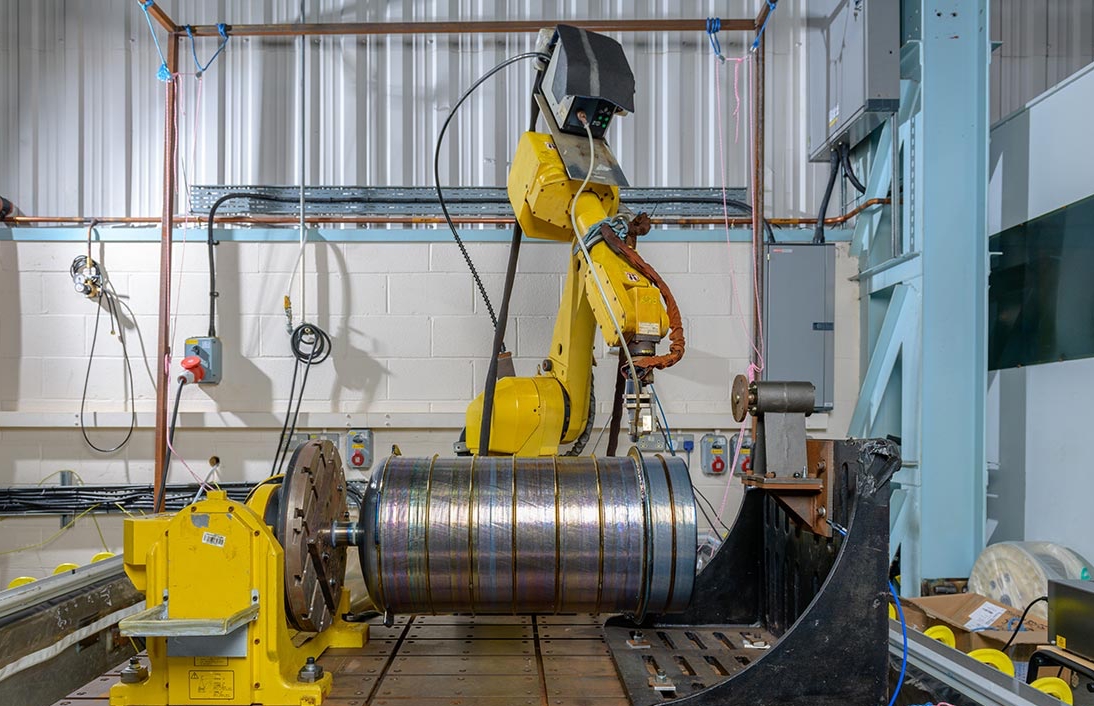
Wire Arc Additive Manufacturing, or WAAM is becoming increasingly popular as a way of creating medium- to large-sized metal 3D printed components. However, how can the mechanical integrity of such new printed parts be ensured?
Porosity - powder-based fusion versus WAAM
The biggest threats to mechanical integrity come in the form of porosity and fusion defects. When it comes to powder-based fusion and WAAM, there is a fundamental difference between the porosity of the materials used in both processes. For instance, powder particles could have pores in them; these have a tendency of remaining in the final part. On the contrary, the wire feedstock used for WAAM has inherently better integrity and no porosity.
In addition, to overcome the issue of porosity in powder-based metal components, hot isostatic pressing is traditionally used to heat and implode any holes and restore the part’s density. However, specialised machinery is required to complete this post-processing step, subsequently limiting the size of component that can receive such remedial treatment.
Overcoming fusion defects
As well as porosity, mechanical integrity can be impacted by fusion defects. Such defects can occur in powder-based fusion, as the particles differ in size and their unevenness can result in voids in the material. Fusion defects can also occur in WAAM components if the deposition of the beads of feedstock do not overlap properly, creating potential mechanical integrity issues. It is essential therefore that an understanding is gained of the behaviour of the wire feedstock material in its molten state, to enable accurate process parameters to be set, and correct geometry to be achieved during printing. If WAAM process parameters are accurate, then any fusion defects in the finished component will be well below pre-set defect size thresholds.
To ensure robust process parameter setting, here at WAAM3D we have three different but complementary methods of analysis that can be used to ensure the creation of accurate parameters:
1. Empirical analysis
2. Numerical solutions
3. Advanced simulation techniques.
WAAM mechanical integrity in practice
Excellent mechanical integrity has been demonstrated using WAAM for titanium pressure tanks designed for use in space exploration. The full case study can be found here. In summary, the WAAM shape was manufactured at Cranfield and then sent to Glenalmond Technologies where it was stress-relieved, laser-scanned, machined and inspected using an ultrasonic method.
With regards to mechanical integrity, the final inspection of the titanium pressure tank was performed by Agiometrix using a computer tomography (CT-scan) for internal quality analysis and an optical scanner, with Thales Alenia Space ensuring that the part met the mechanical requirements and specifications. Following the checks, the project team confirmed that the vessel fulfilled the driving technical and quality requirements.
If you have any questions on WAAM and mechanical integrity or have a project that our Team can help with, get in touch.