Advanced Technology.
Advanced Hardware.
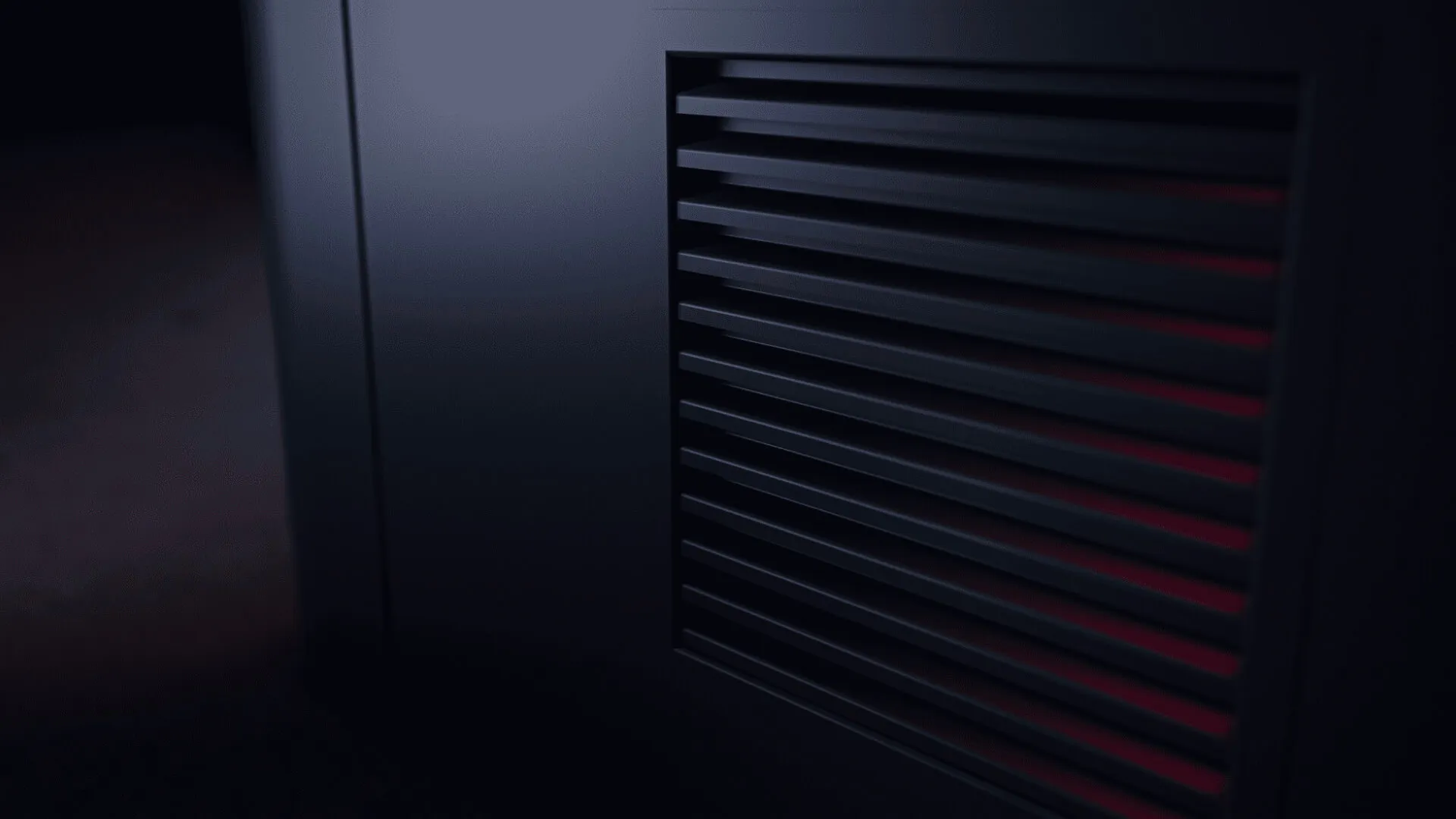
The manufacturing process of the future cannot rely on hardware from the past.
From sensors to end-effectors and automation to health & safety, we have put you, the user, at the core of our hardware design process. We have redefined what state of the art means, in and around the deposition volume, to give you the best possible experience. What’s more, it all comes together in a vehicle through which we enable you to make the best possible parts: RoboWAAM.
THE HARDWARE
RoboWAAM XP
01/07
RoboWAAM® XP
Introducing RoboWAAM® XP: the latest in large-format WAAM technology, featuring our patented CWGMA multi-wire process for industry-leading control and efficiency. Achieve deposition rates up to 15 kg/h with 5x process speeds, while maintaining exceptional quality and precision. RoboWAAM® XP supports MIG, MAG, and CMT for unmatched productivity and performance.
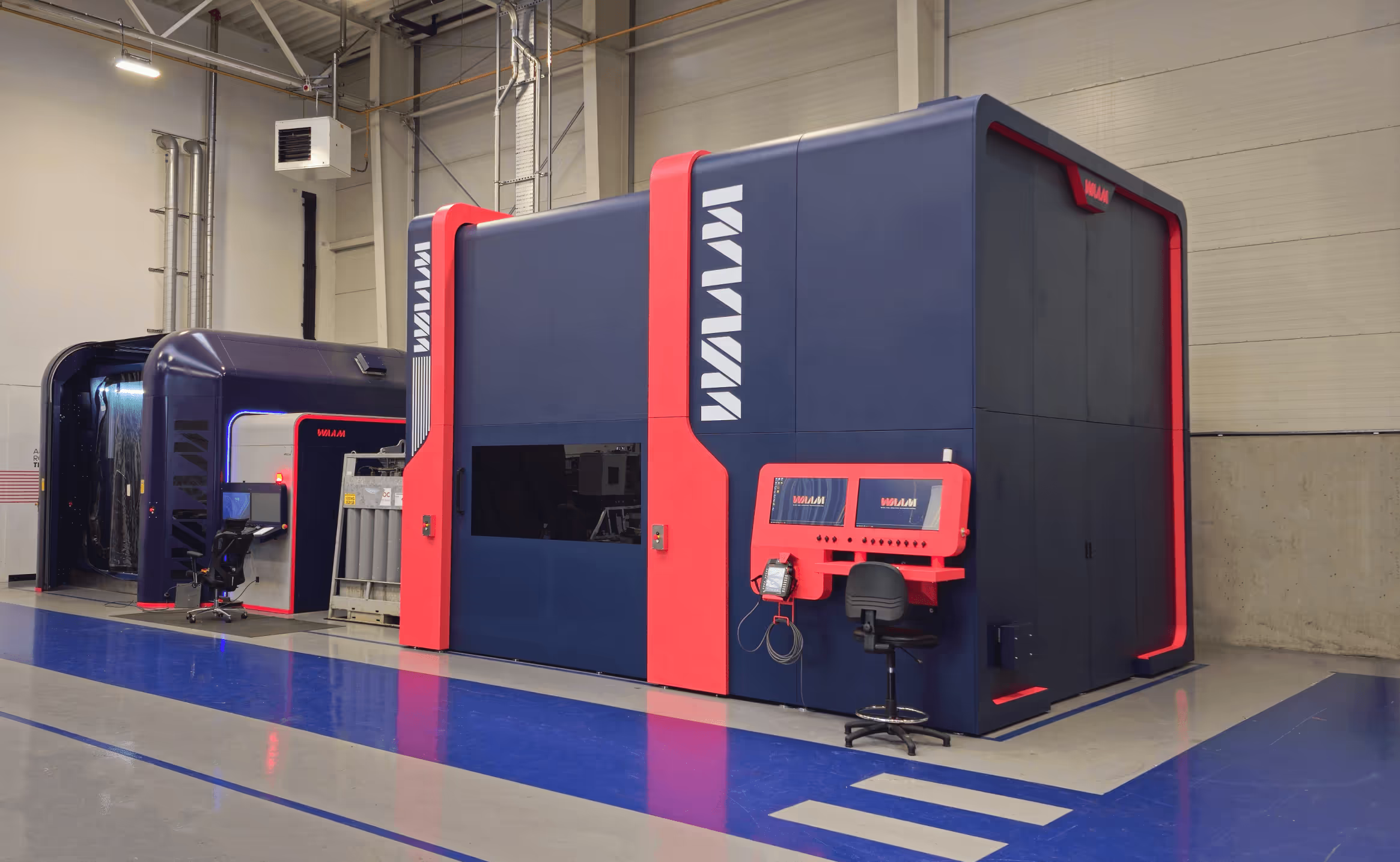
RoboWAAM® Advanced
02/07
RoboWAAM® Advanced
The best features of RoboWAAM® Advanced are the ones you do not see: on board fumes treatment, automatic deposition environment purging, quick wire changeover system, and the 40 sensors keeping an eye on the key process variables, tens of times per second.
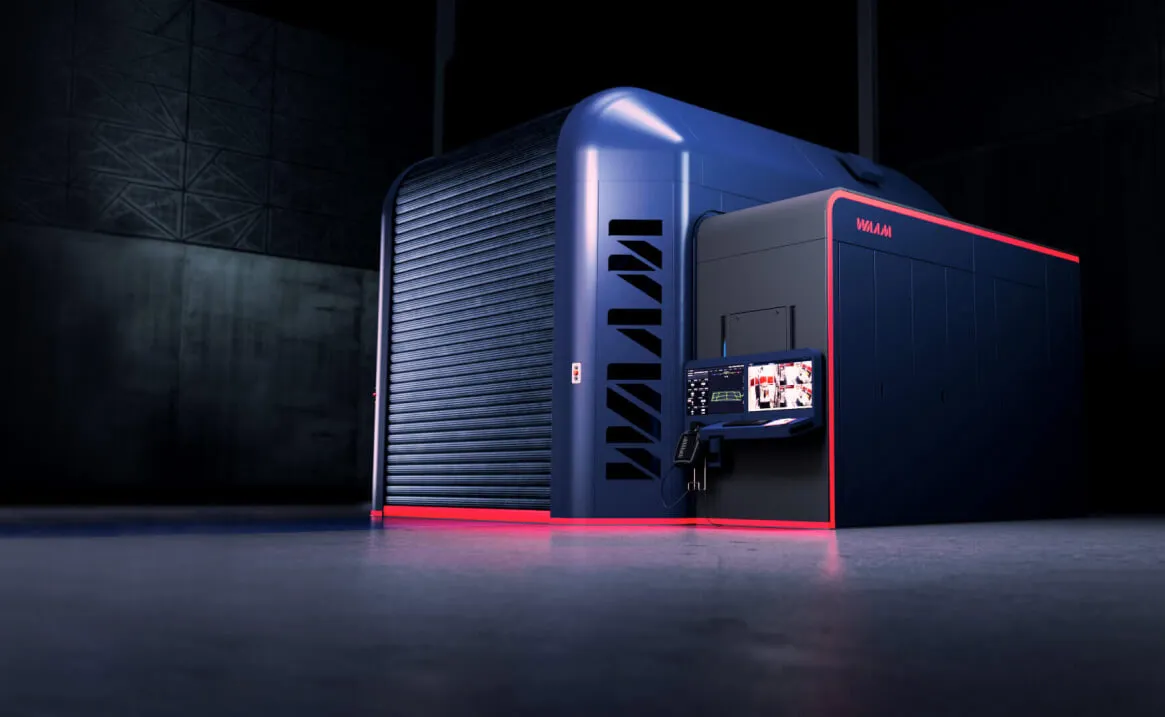
miniwaam™
03/07
MINIWAAM®
The MiniWAAM® system is a compact platform designed to seamlessly integrate Wire Arc Additive Manufacturing into your manufacturing workflow, cost effectively.
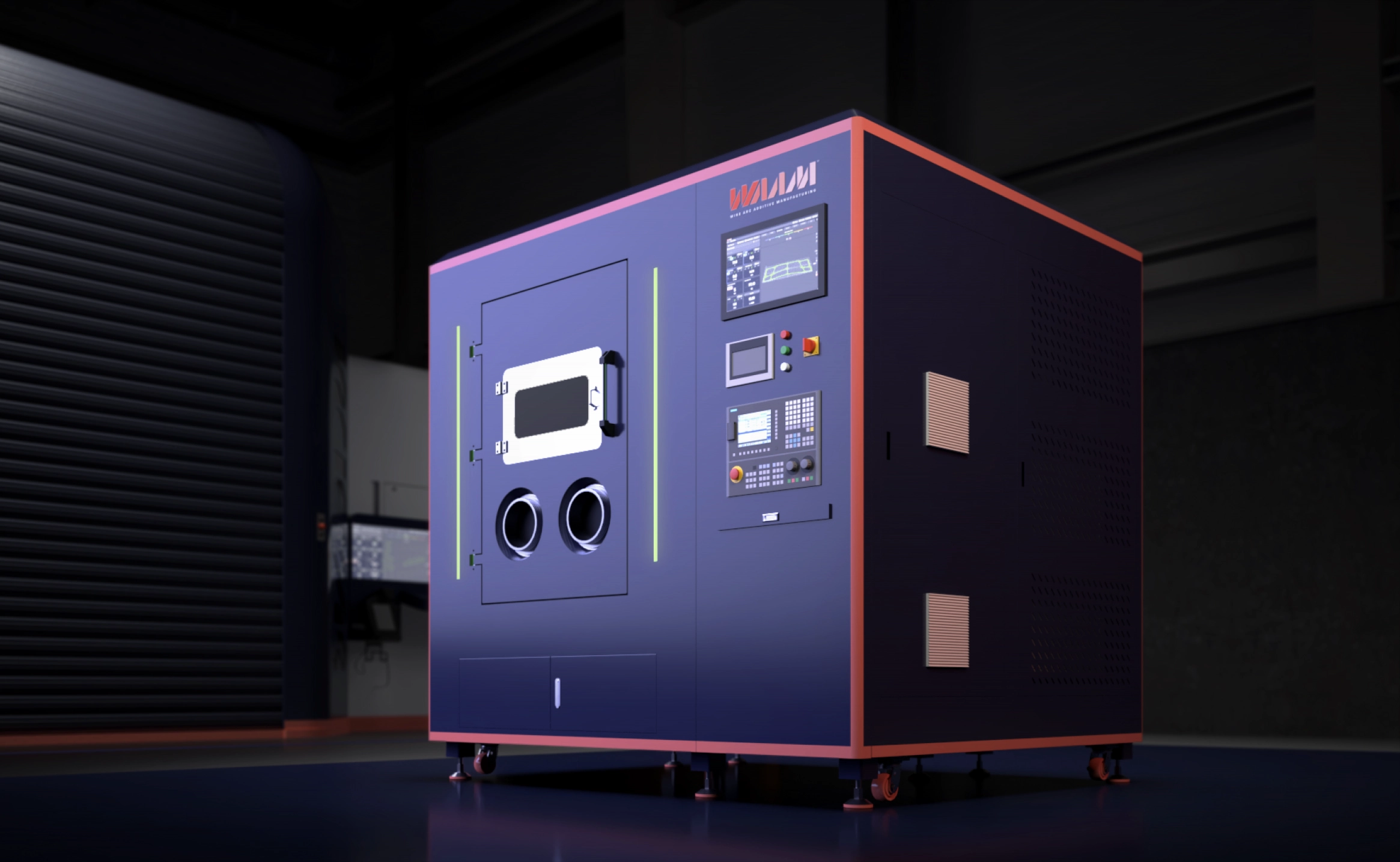
END EFFECTORS
04/07
Technology packs
Upgrade your existing robotic systems with our Technology packs. They include end effectors to print and monitor, power sources, wire feeders, and the software to programme and control the deposition.
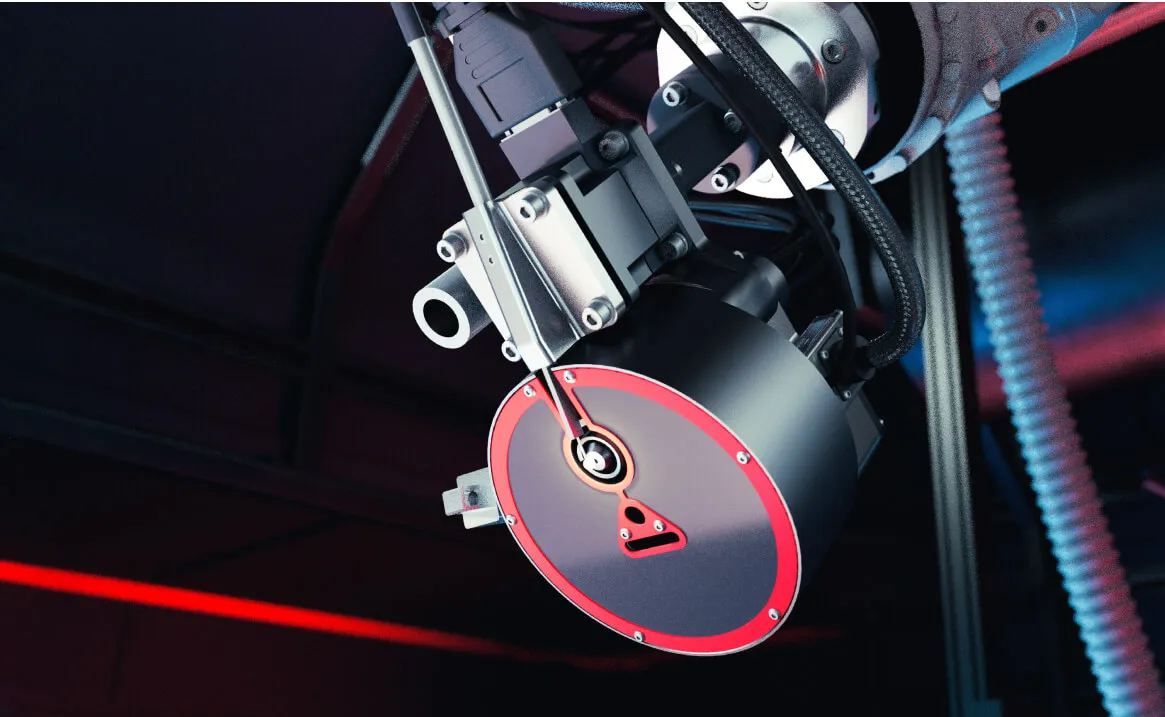
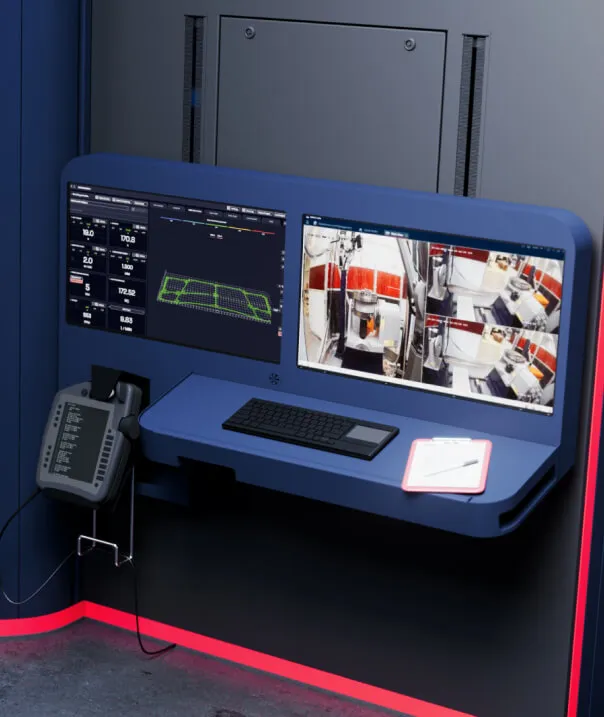
RoboWAAM™ SYSTEM
05/07
RoboWAAM™ System
RoboWAAM is the result of two decades of R&D work, printing component after component for particularly challenging projects across several industries. Our most meticulous stakeholders have informed our vision for an integrated system which can do what it says on the tin: deliver excellent parts.
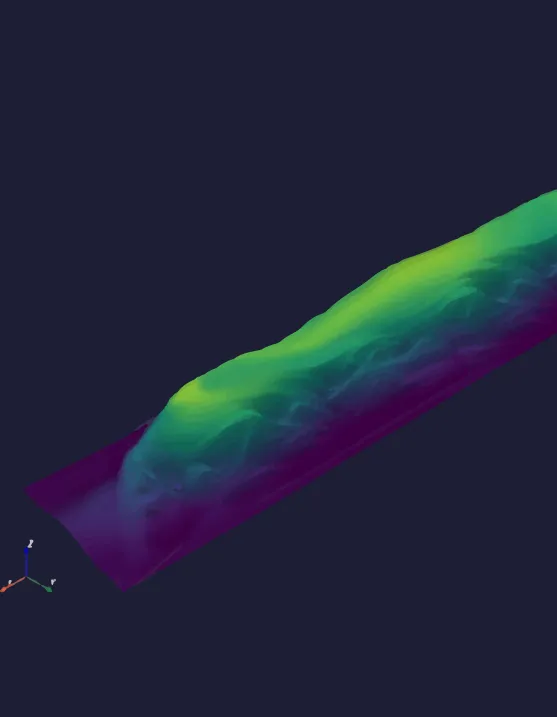
ShapetechTM
06/07
ShapetechTM
Across the many firsts featured on RoboWAAM, ShapeTechTM is the most impressive. Say goodbye to laser scanners or touch probes. ShapeTechTM is powered by interferometric technology to provide real-time geometrical data, stored on WAAMCtrl®’s server and shown within WAAMCtrl® process dashboard. Not just the layer height, but the full 3D profile of what you are depositing, live.
PROCESSES
07/07
Deposition processes -
Plasma and CMT
Depending on your requirements in terms of a part’s materials and geometries, together we can select the most suitable WAAM process to power your RoboWAAM.