The complete guide to Direct Energy Deposition (DED)
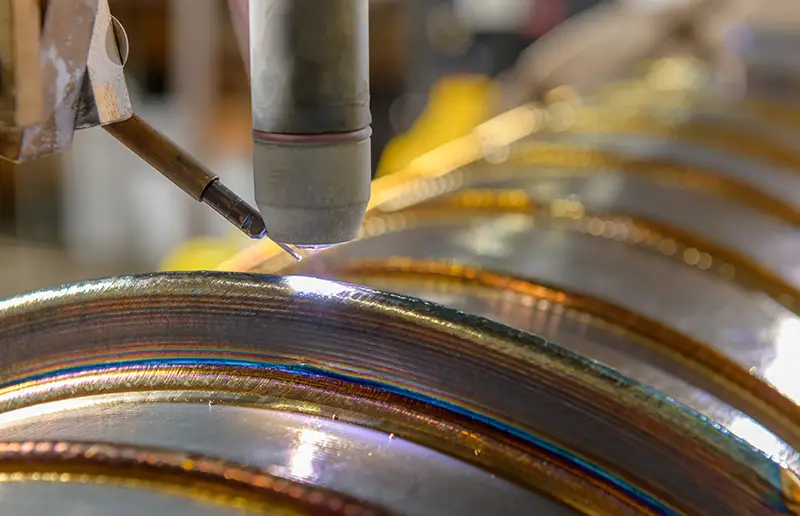
From prototyping to production cycle efficiency Directed Energy Deposition is helping manufacturers respond to a rapidly changing manufacturing environment. Direct Energy Deposition (DED) processes are versatile and powerful additive manufacturing methods due to their rapid deposition, versatility of materials and large-scale production capacity. The DED process can produce exceptionally large structures, making it an ideal choice for applications that require scalability and robustness. Here is a complete guide to DED 3D printing technologies, the materials suitable for DED, different DED processes, DED and applications and where Wire Arc Additive Manufacturing fits into the picture.
What is DED?
DED is a 3D printing process that involves the melting or sintering of a material (typically in powder or wire form, using a heat source such as a laser or electron beam) to build up or repair a part layer by layer. It allows complex internal structures and intricate geometries to be fabricated and the end result is astable and strong structure. DED's capability to produce optimised designsis also ideal for designers looking to create and iterate prototypes quickly. Find out more about different DED processes including electron beam DED, WAAM andLMD, benefits and challenges here.
Materials suitable for DED processes
DED can be used to deposit metals in 3d printing wire, powder or ceramic form. Virtually any weldable metal can be 3D printed, including titanium and its alloys, Nickel, tantalum, tungsten, niobium, stainless steel and aluminium. The wide variety of materials that can be used withDED makes it an ideal choice of process for a wide range of manufacturing scenarios.
DED processes and applications
DED processes commonly used in material development composition include:
· Laser Metal Deposition (LMD) – which is versatile and can be used with a variety of metal alloys. It relies either on blown powder, or wire feed stock
· Wire Arc Additive Manufacturing (WAAM®) – which can use a range of materials including titanium, aluminium, refractory metals, steel, bronze and copper to Invar®, Inconel® and magnesium. There are a few WAAM variants, including Plasma Arc Deposition (which allows for the more precise deposition), Metal Inert Gas, and the novel Cold Wire MIG (CWMIG®).
DED technologies enable additive manufacturers to create a wide range of high-value components. It is also used to enhance surfaces by applying coatings or claddings to bolster wear resistance, alter surface properties and combat corrosion. This blog on DED processes and applications can help you better understand how DED processes can be applied to situations in your manufacturing process.
DED’s versatility: A game changer for Medical, Aerospace, Defence and many more industries
From medical and automotive to tool and die, DED’s ability to create complex structures is being maximised. Industries in rail, energy, marine, defence and oil and gas are also tapping into the high-value component creation, modification and repair potential of DED. In particular, DED processes have revolutionised aviation component manufacturing. Looking at DED and aerospace, its capability to create lightweight, optimised designs makes it ideal for the production of aerospace components, including wing spars, wing ribs, landing gear structures, turbine blades, air foils, and engine casings.
Factors to consider when choosing the right DED 3D Printing Process
When choosing the right DED 3D printing process, there are many factors to consider. These include the build size, volume and material characteristic requirements of the end component, and the surface finish, accuracy level and detail required. Other factors to influence DED choice include speed of production and return on investment.
Analysing cost efficiency and ROI of DED process
3D printing DED processes can be profitable and efficient solutions. However, it is important to analyse front-end investment compared to back-end returns - such as speed to market and material usage efficiencies - to discern which DED process will yield the best results. A key factor in evaluating DED's economic impact is its ability to generate concrete returns on investment (ROI). One of the issues faced by additive manufacturers today is whether the latest DED technologies will pay off. This blog examines the production costs, material usage efficiencies, and other factors that will affect the outcome -
WAAM sets new standards in DED
WAAM is a cost-effective method compared to other DED processes. It enables the creation of high-quality components with material utilisation close to 100%. Very large part sizes and more complex design features, such as internal cavities, can also be incorporated. WAAM has exceeded other DED techniques in terms of understanding, potential deliverables and production and cost efficiencies. WAAM solutions can now offer manufacturers high levels of process control, robust evaluation, increased deposition rates and complexities and cost-effective production.
WAAM Technologies Providers
When looking to choose the correct WAAM technology provider, it is important to look at a range of factors. These include getting answers tothe following questions:
· What is the provider’s level of technical expertise and experience?
· What depth of functionality and flexibility can their WAAM software and WAAM hardware offer?
· What are the performances their solution can deliver vs other competitors, and at what cost?
· What level of process monitoring, and control is available, so that consistent quality and certification and regulatory requirements can be met?
· Is their technical support robust and what is their reputation within WAAM and academic communities?
· Are there any knowledge transfer or training programs offered by the provider that will help you maximise the use of WAAM?
DED is opening up exciting opportunities for additive manufacturers; from repairing critical components to creating intricate parts and prototypes, DED 3D printing processes are valuable in a wide range of industries thanks to their adaptability and precision. DED processes are expected to expand into new industries and be utilised in innovative ways as technology advances and processes are improved.
Contact us if you would like to learn more about new trends in DED additive manufacturing and WAAM's potential for improving your manufacturing process. We are happy to assist you.