Wire Arc Additive Manufacturing Enables Waste, Footprint and Cost Reduction
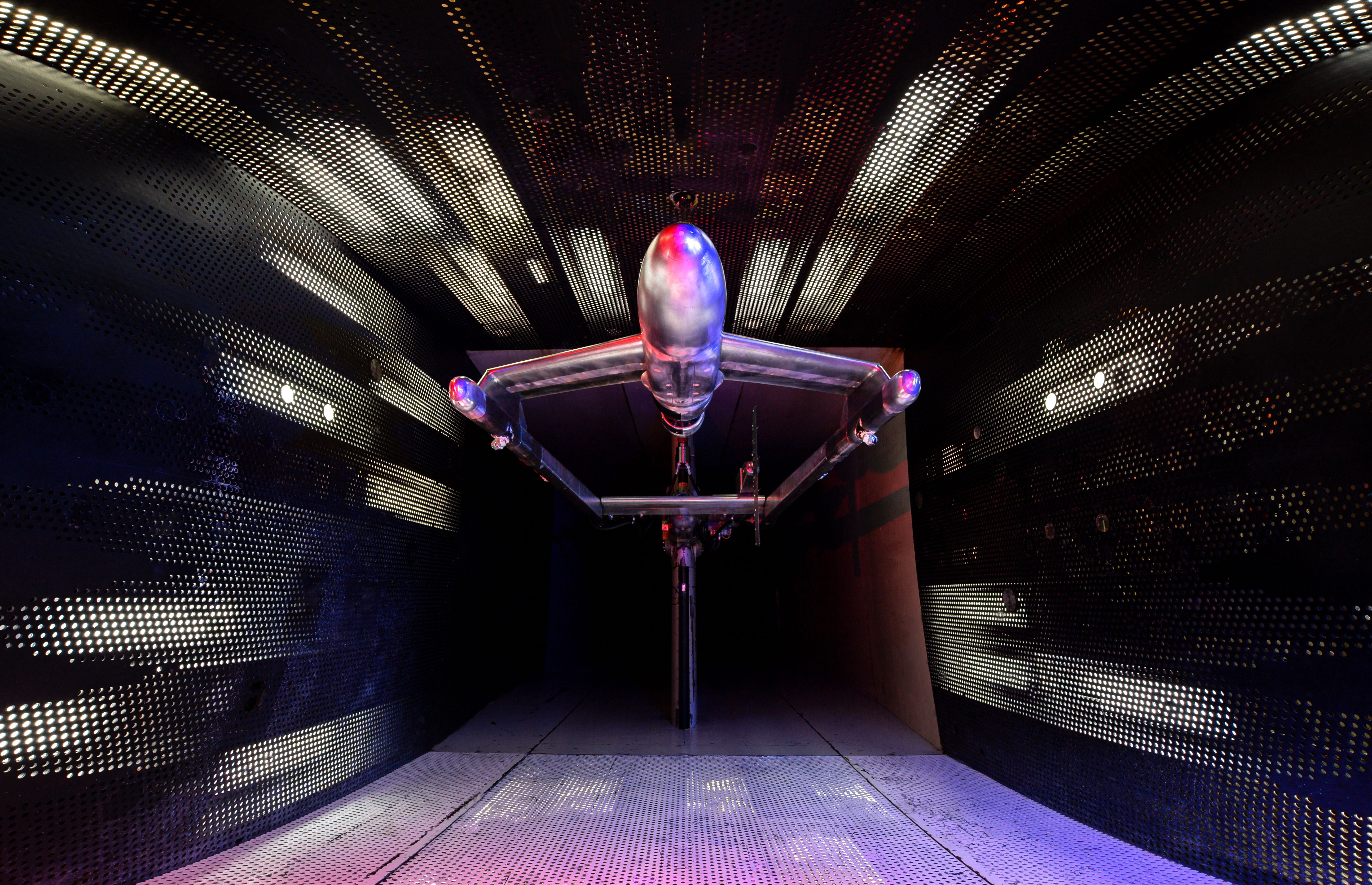
The triple bottom line is gaining momentum in companies across the globe as more and more businesses are trying to ensure that they deliver not just on profit, but on social and environmental issues as well. This is now featured amongst the top challenges manufacturers face right now.
Top manufacturing challenges
- Reshoring manufacturing to mitigate risk
- Protecting profit margins against inflation
- Designing products for sustainability
- Launching products faster and accelerating operations
Additive manufacturing’s role
Additive manufacturing’s ability to deliver customisable components, with a high degree of material utilisation, minimum fixed costs and environmental benefits has made it increasingly popular with manufacturers. When it comes to creating large-scale metal components, wire-arc additive manufacturing (WAAM) has been shown to demonstrate some of the most significant potential for time, cost and environmental savings in both component fabrication and repairs.
WAAM reduces waste and swarf
Despite closed die forging making huge strides forward in terms of reducing material wastage, traditional forging still leads to high material wastage. WAAM can significantly reduce the amount of material wasted on component creation. A case in point:
- In the Aerospace industry, the buy-to-fly (BTF) ratio is the ratio of the mass of the starting billet of material to the mass of the finished part that is flown on the aircraft. The smaller the ratio, the less material is wasted. The BTF ratio for aero engine components can be as high as 25, and WAAM can reduce that ratio to <2.
WAAM reduces pre-machining wastage
The moulds and dies used for forging and casting can have long procurement times and high costs. Due to lead time and design cycle pressures, the purchase of tools can begin before the part’s design has been finalised. To overcome this, many manufacturers add a larger waste envelope into the final geometry of the mould or die, leading to increased levels of material waste to achieve the final product. As WAAM is a digital manufacturing process it requires no tools – apart from the clamps needed to fix the starting feedstock – so the upfront non-recurring cost is virtually eliminated, and design changes can be made whenever needed, eradicating additional geometry waste.
WAAM reduces spare part wastage
For spare part, inventory management and stockkeeping there are two types of potential waste: the material itself, if the part isn’t needed, and the energy embodied into the part. Unused stock can lead to significant financial and material waste. Rather than keeping stock that might not be needed, more manufacturers are choosing WAAM. This helps them reduce inventory and logistics costs by focusing on local, on-demand manufacture and helps them to resolve spare part production and repair issues, quickly and as cost-effectively as possible.
WAAM improves environmental performance
Because of the material savings achieved using WAAM, a manufacturer’s environmental performance can be improved when it comes to component creation and repair. WAAM has long been used to repair structures, extending the life of components, and delivering significant energy and CO2 emission savings. Additional environmental benefits can be unlocked by having local WAAM centres, thus reducing the impact of logistics.
The WAAM process minimises waste, and material-usage for this process is very high at around 98%. For those manufacturers looking to demonstrate that they are taking the triple bottom line seriously, it is an important part of the large-scale metal component fabrication toolkit.
For more information on how WAAM can help improve your triple bottom line get in touch.