3D Component Printing Encourages Smooth Running for Marine Applications
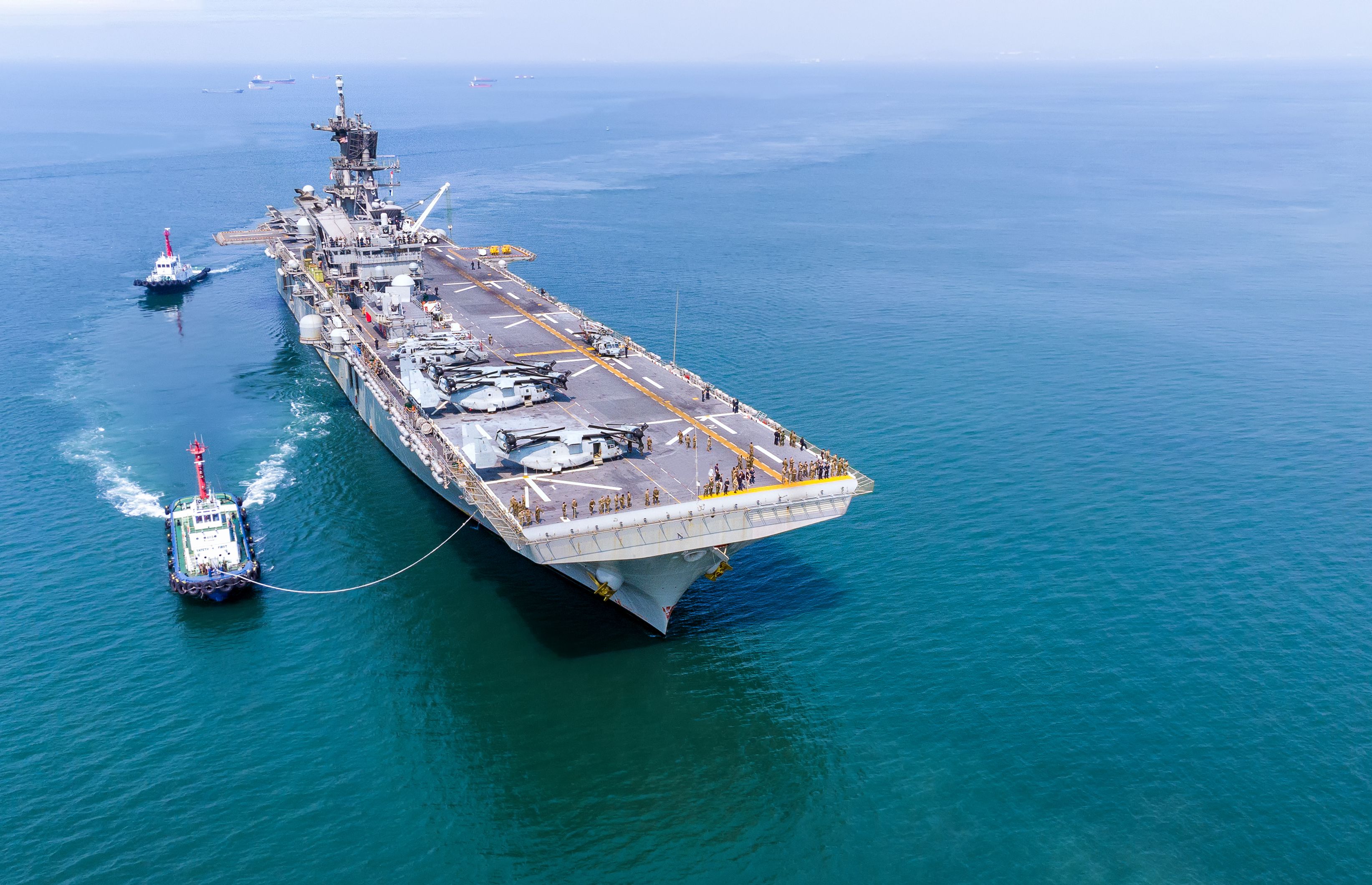
According to an industry survey by the IMarESTi, the three biggest challenges facing the marine industry in 2023 and beyond are people, technology and the environment. Not surprisingly for many marine professionals attracting and retaining personnel and overcoming the growing skills gap is a major short and long-term concern. Alongside this is the ability to embrace technology and adapt to changing environmental demands.
Two of the technology challenges cited by respondents to the survey were: ‘Keeping up with the pace of change’ and ‘leveraging technology …to improve margins and efficiency’. This is something that we at WAAM3D are hearing more and more from concerned industry leads looking for efficient ways to manage their component supply. So how can 3D printing help marine companies keep their operations running smoothly?
3D printing growing in popularity
3D metal component printing for both fabrication and repairs is already beginning to prove its worth to marine operators across the globe. Wire arc additive manufacturing (WAAM) can be used to create or repair large-scale metal components and is ideal for propellers, liners, bearings, shafts and large brackets. WAAM offers multiple technical and operational benefits and can be used to:
- Significantly reduce lead times – to weeks or less - and replace long lead-time processes, such as forging and casting
- Repair parts quickly and simply at – or close to – the point of use and avoid the scrapping of large quantities of materials because of relatively small damages
- Reduce manufacturing costs and waste – including the cost of tooling and other non-recurring costs
- Enhance the physical properties of critical components
- Optimise your manufacturing supply chain
- Reduce the environmental impact of manufacturing operations. A recent Life Cycle Assessment (LCA) of a demonstrator part from a maritime supplier, carried out by WAAM3D in partnership with Cranfield University, quantified a 40% reduction in environmental impact when made by WAAM as opposed to traditional forging + machining + fabrication.1
WAAM as part of maintenance toolkit
WAAM offers significant repair potential within periodic or scheduled maintenance. This is because worn component surfaces can be proactively rebuilt, before catastrophic damage occurs. However if a stoppage does occur due to a damaged component, WAAM can also be used to repair the broken or damaged part in situ, rather than waiting a long time for a replacement part. Thanks to WAAM’s ability to fully melt the wire feedstock, which subsequently becomes part of the final structure, exceptionally high levels of mechanical integrity are created.
WAAM typically reduces lead times from possibly a year or more, to a few weeks or less. It can also facilitate the reduction of inventory and logistics costs by focusing on local, on-demand manufacture; helping marine operators to resolve spare part production and repair issues, quickly and as cost-effectively as possible. When it comes to ‘leveraging technology to improve margins and efficiency’, WAAM is becoming an important tool in the large-scale component fabrication and maintenance toolbox.
WAAM offers a range of benefits to marine operators. For more information on how WAAM can benefit you, get in touch.