Application-Specific DED Processes
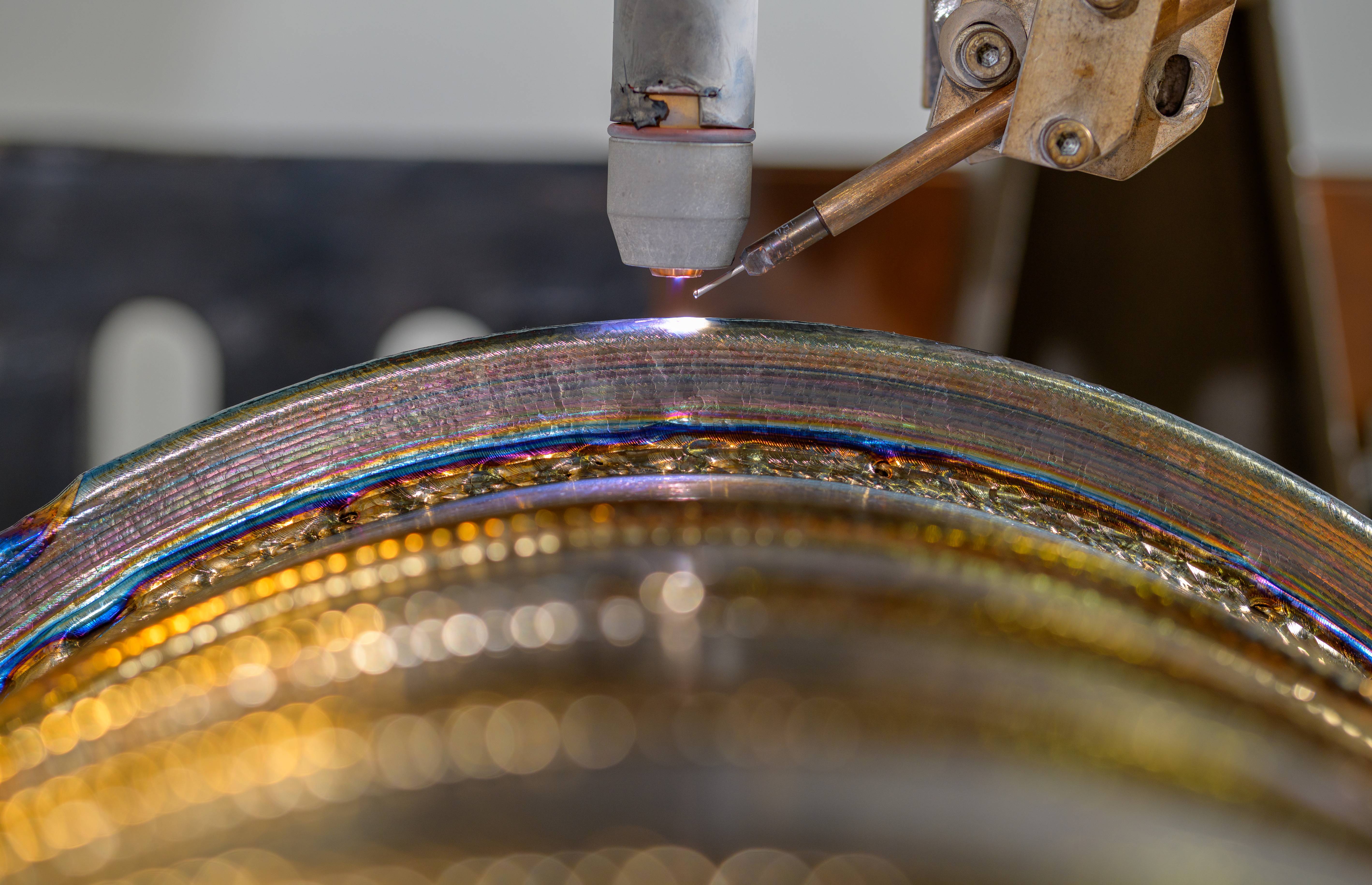
DED processes and how they can be applied to a variety of situations
As additive manufacturing technologies continue to evolve, finding the right Direct Energy Deposition (DED) process for your needs becomes increasingly important. Production efficiency, cost effectiveness, and quality of manufactured parts are all dependent on this choice. A well-chosen method - whether Wire Arc Additive Manufacturing (WAAM) for large-scale applications or Laser Metal Deposition (LMD) for intricate designs - ensures optimal material usage, reduced waste, and conformance to precise specifications. Taking informed decisions enables manufacturers to meet industry regulations, as well as catalyse innovation, paving the way for advanced manufacturing technologies.
Here, we will examine DED processes and how they can be applied to a variety of situations.
1. DED for customised material development
DED processes are flexible in material selection, allowing the incorporation of various elements or alloys to achieve desired characteristics. Using these additive manufacturing methods, tailored materials can be created with specific compositions, properties, and functionalities. DED facilitates the development of materials that are optimised for specific aerospace, automotive, biomedical, and other applications.
Novel material compositions can be explored, and material properties refined for specific applications, using alterations in powder composition, laser or electron beam power, wire properties and layer thickness’ etc.
DED processes commonly used for material development customisation include:
- Laser Metal Deposition (LMD) – which is versatile and can be used with a variety of metal alloys.
- Wire Arc Additive Manufacturing (WAAM®) – which can use a range of materials including titanium, aluminium, refractory metals, steel, bronze and copper to Invar®, Inconel® and magnesium.
- Plasma Arc Deposition – this is a subset of WAAM, which allows for the more precise deposition of the same materials mentioned above
- Blown Powder Deposition – which is adaptable to various materials, including metals and ceramics.
Customised material development using WAAM – our expertise
WAAM3D is highly experienced at developing new chemistries that match the required process; with a series of signature aluminium-based alloys, with the addition of scandium and other niche elements that work extremely well with the WAAM process.
Alongside Cranfield University, WAAM3D has been highlighted as a Key Innovator by the European Commission’s Innovation Radar for the joint work done on creating multi-material add-on software for WAAM systems. This brings even more material development customisation to end users because the two wire-feeders that feature in the process can be used to supply the same wire, or different alloys, thus upgrading RoboWAAM® to multi-material capability. Interested in learning how WAAM3D can assist you with your unique material development requirements? Contact us today.
2. DED for cladding and coating or repair
Various DED processes specialise in enhancing surfaces by applying coatings or cladding to bolster wear resistance, combat corrosion, or alter surface properties. Some methods repair existing components better than others. Each technique involves distinct materials and application methodologies, with selection based on material prerequisites, substrate traits, and specific application demands.
The versatility of DED processes empowers industries to fortify surfaces against wear and corrosion, offering tailored solutions for surface modification and component refurbishment.
DED processes commonly used include:
- Laser Metal Deposition (LMD) – melting and depositing the material onto the substrate and used for repair, cladding, and additive manufacturing (AM).
- Wire Arc Additive Manufacturing (WAAM) – a continuously fed wire is melted onto the substrate using an electric arc and is used for tooling and the cladding and repair of large-scale components. This includes Plasma Transferred Arc (PTA), in which the plasma arc transfers material from a consumable electrode to the substrate and can be used to create wear-resistant coatings for corrosion protection and the repair of high-wear components.
- Electron Beam Freeform Fabrication (EBF3) – the electron beam melts and deposits material and is used in the repair and fabrication of large-scale components.
- Cold Spray - high-velocity solid-state particles impact a substrate and create a coating without melting the material, making this process useful for coating temperature-sensitive materials, corrosion protection, and repair.
WAAM3D and Cranfield University have developed a next generation high-productivity variant for Wire Arc Additive Manufacturing (WAAM). The process offers fully independent material and energy feed rates and as well as significantly improving productivity has been shown to reduce dilution - even when used for cladding applications.
You can learn more about the benefits of the WAAM process for repair by reading this blog
3. DED for high-value component manufacturing
DED processes are particularly valuable for high-value component manufacturing across various industries, including aerospace, oil and gas, defence, and power generation, since they can produce intricate, large, or complex parts with precision. For high-value component manufacturers, DED processes offer precision in material deposition, the ability to work with a variety of materials, and the ability to create large and complex parts with reduced waste. These processes contribute significantly to cost-effective production, reducing lead times, and enabling the fabrication of parts that meet stringent quality and performance standards.
DED processes commonly used for high-value component manufacturing include:
- Laser Metal Deposition (LMD): This process involves melting and fusing metallic powders with a laser.
- Electron Beam Additive Manufacturing (EBAM): EBAM uses an electron beam to melt metal powder and layer-by-layer produce 3D shapes.
- WAAM (Wire Arc Additive Manufacturing): WAAM uses an electric arc to melt wire feedstock, which is then deposited layer by layer to build up the part. The process can be incredibly fast and cost-effective when it comes to larger components.
The adaptability and precision of DED processes make them valuable in various industries for a wide range of purposes, from repairing critical components to creating intricate parts and prototypes. As technology advances and process improvements continue, DED processes are expected to expand into new industries and innovative uses.
Stay tuned for more information on new trends in DED additive manufacturing. Contact us if you're interested in learning more about Wire Arc Additive Manufacturing DED and how it can be used for your business requirements.