Reducing Component Part Costs Using WAAM
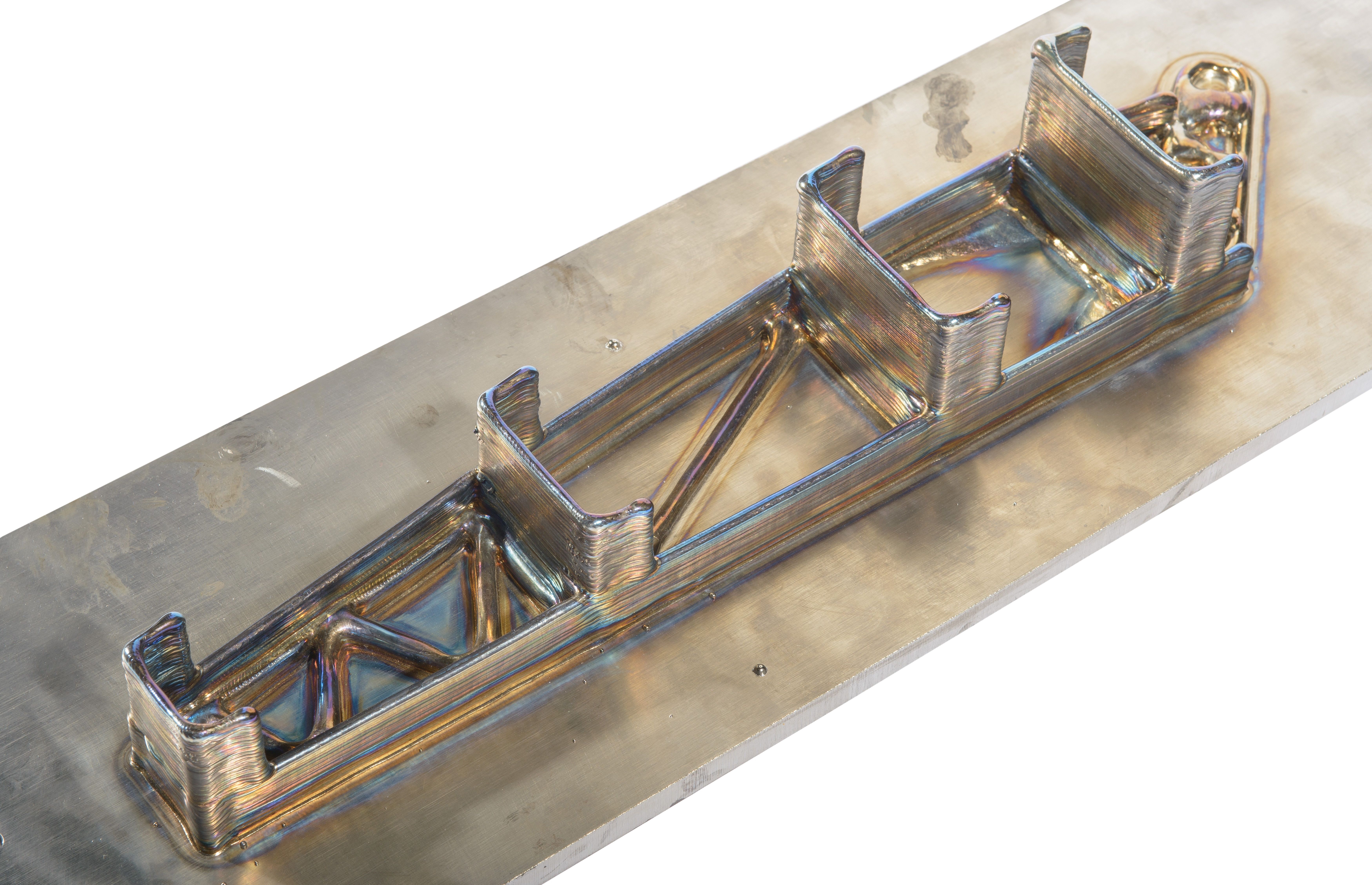
Wire arc additive manufacturing (WAAM®) or directed energy deposition (DED) additive manufacturing is being considered more and more in the creation and repair of medium-to-large- components. The process delivers many benefits, one of which is its potential to reduce parts costs for manufacturers. How does WAAM do this?
Reduced raw material usage
Under most circumstances, WAAM has been shown to be a more economic option than machining components from solid. This is due to its excellent buy-to-fly raw material reduction. Subtractive manufacturing leads to most of the material ending up as swarf. However, with the latest in 3D-printing technologies such as WAAM, this waste can be reduced significantly, and with it costs too. This is because WAAM delivers a reduction of the buy-to-fly ratio[1] (BTF) to <2 (Dutta & Froes 2017), which leads to cost savings of up to 70% compared to machining from solid.
Reduced energy consumption
Large energy efficiencies can be achieved using additive manufacturing compared to machining from solid. Moreover, although electricity is considered as a relatively minor factor of the total cost, WAAM processes achieve much higher energy efficiencies (70%) than other additive manufacturing processes such as Electron Beam Powder Bed Fusion (EBPBF) (20%) and laser technologies(5%) as shown here:

Lower operating and maintenance costs
When selecting additive manufacturing equipment, the cost of machinery, operations and maintenance need to be considered. Comparing AM solutions, powder-feed equipment requires more maintenance than wire-feed (Sames et al. 2016), to ensure humidity levels, shielding gas and temperature are all at appropriate levels. Also, the capital investment in EBPBF and laser powder bed fusion (LPBF) technologies is greater than WAAM.
Here is a cost comparison of the four principal additive manufacturing processes:
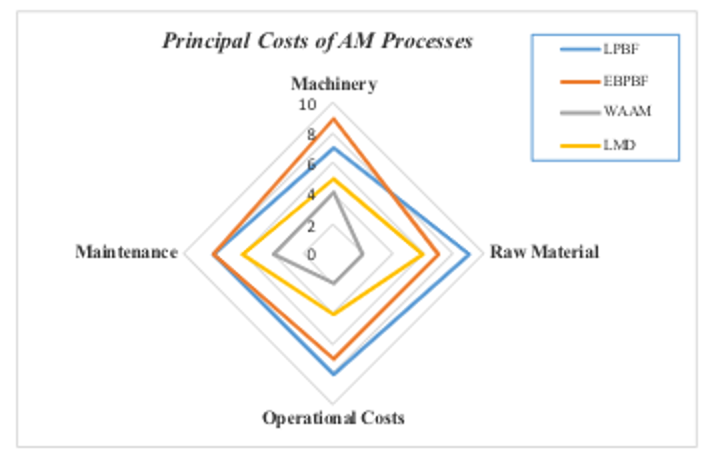
When it comes to reducing part costs, AM processes have a huge part to play in industrial, oil and gas and aerospace applications. As the below comparison shows, choosing the best AM process depends on what build rate, accuracy, surface finish, complexity and size is required, but for medium- to large-scale components, WAAM has the potential to deliver significant part cost reductions.
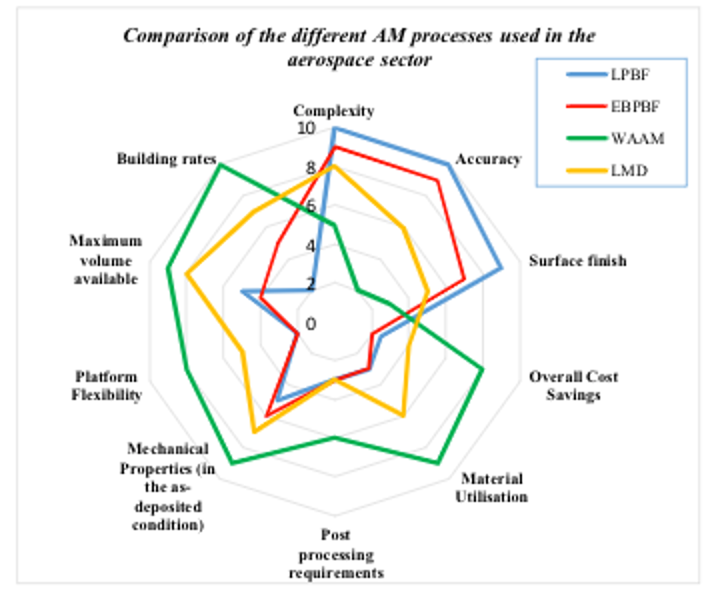
To find out more about how to reduce part costs, why not see how WAAM can help you? For more information on how WAAM can benefit you, contact us here.
[1] The buy-to-fly ratio is the ratio of the mass of the starting billet of material to the mass of the final, finished part.