The Role of DED Additive Manufacturing Technologies in Aircraft Component Manufacturing
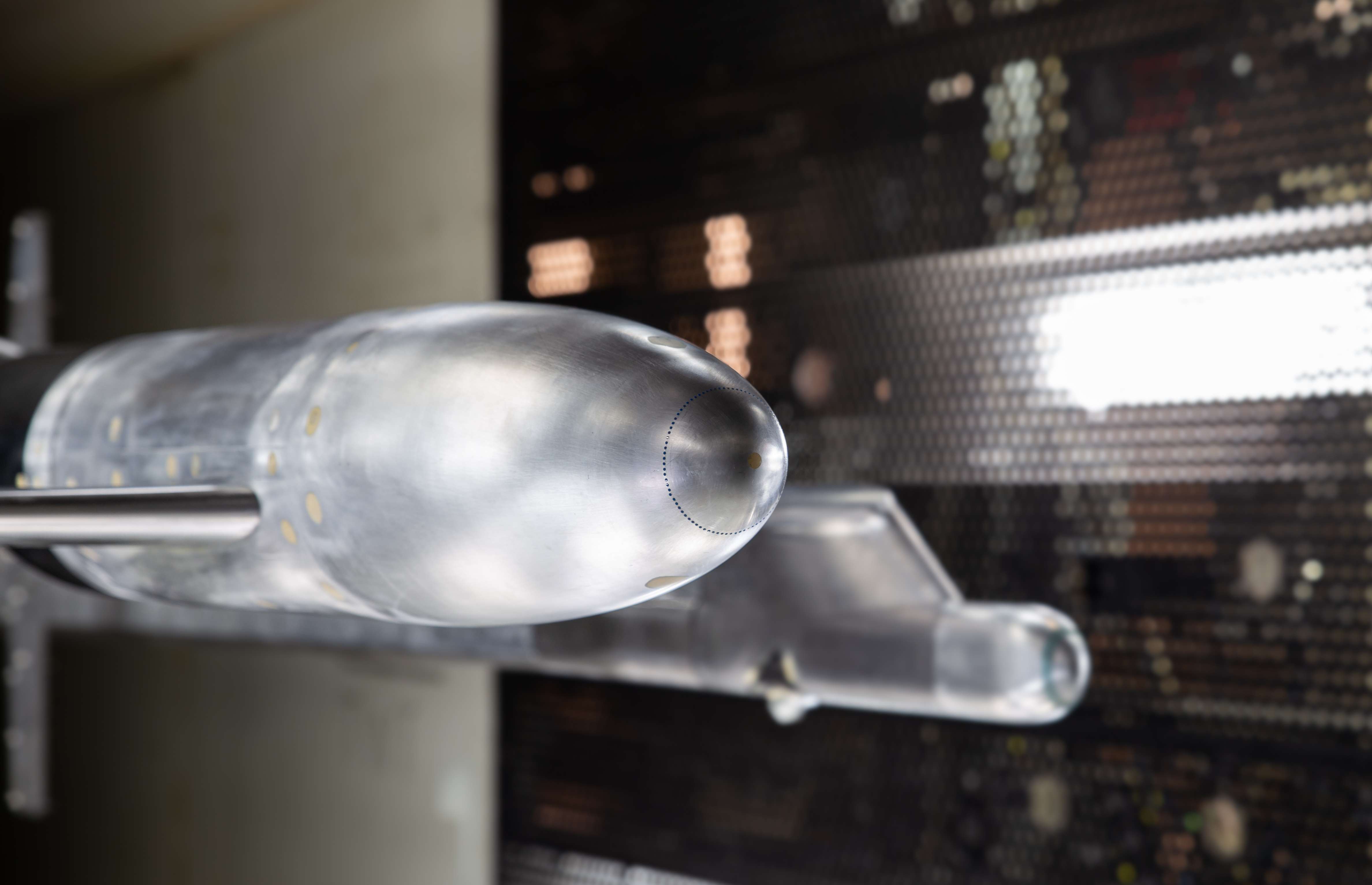
With the space market predicted to grow to $1 trillion by 2030[i] and hypersonic aircraft development well under way, the aerospace sector is at the forefront of technological and engineering developments. As the boundaries of existing design continue to be explored however, more traditional manufacturing and design processes are struggling to keep up with these advancements in aircraft component manufacturing. This is where Directed Energy Deposition (DED) technologies have a significant part to play in the future of aerospace.
The Directed Energy Deposition (DED) technologies have opened new avenues for aerospace design creativity. In this blog, we look at how DED additive manufacturing revolutionises aerospace component production.
Rapid Prototyping Capabilities
DED allows manufacturers to experiment with new concepts and modify quickly, accelerating innovation. With DED's additive manufacturing process, designers can quickly create prototypes and custom components. It enables manufacturers to test new designs, refine them in response to performance feedback, and iterate rapidly until they find the right solution.
DED reduces the time-to-market for new aircraft and components by significantly shortening the product development cycle. Furthermore, the ability to customise parts on-demand allows manufacturers to respond swiftly to changing market demands and customer requirements, enhancing their competitiveness in the aerospace industry. As a result of DED's flexibility and rapid prototyping capabilities, the aerospace industry is advancing into a new era of speed and agility.
Lightweight Structures & Optimised Designs
Directed Energy Deposition (DED) technologies allow wire or metal powder to be deposited layer-by-layer, which allows complex internal structures and intricate geometries to be fabricated. DED's capability to produce lightweight, optimised designs is ideal for aerospace components, including turbine blades, air foils, and engine casings. In addition to improving performance and fuel efficiency, these advancements also ensure structural integrity, revolutionising the aerospace industry's approach to component manufacturing.
Intricate Engine Components
Engine components are one area in which DED shines brightest. Due to their intricate internal geometries and high-performance material requirements, complex turbine blades once posed significant challenges for traditional manufacturing methods. The DED additive manufacturing technologies can be used to design and manufacture turbine blades and other fully dense, near-net shape engine components with internal cooling channels as well as optimised geometries. The intricacies of these systems make engines perform more efficiently and consume less fuel while maintaining structural integrity at the same time.
Optimised Aerodynamic Surfaces
Aerodynamic efficiency is paramount in aerospace design. Through DED AM technologies, designers can create complex, streamlined shapes with precision and accuracy, minimising drag and maximising airflow efficiency. DED enables aerospace manufacturers to optimise aerodynamic surfaces for better flight performance, reduced fuel consumption, and increased range, ultimately advancing the state of modern aviation.
The additive nature of Directed Energy Deposition (DED) opens new possibilities for design innovation, performance enhancement, and efficiency improvements in the aerospace industry. With the advancement of technology, we can expect to see even greater advancements and applications in the quest for safer, more sustainable air travel.
Wire Arc Additive Manufacturing and Aerospace Component Manufacturing
Among the additive manufacturing technologies offered by DED, Wire Arc Additive Manufacturing (WAAM) is one of them. WAAM is proving popular in aerospace component production, due to its potential to create large-scale structures, such as aircraft wings, engine components, fuselage sections and propellant tanks quickly and efficiently. Known for its material efficiency, WAAM deposits the material only where it is needed, minimising expensive material waste. In fact, WAAM’s buy-to-fly ratio[ii](BTF) is reduced to <2, which leads to cost savings of up to 70% compared to machining from solid.
Fast deposition rates enable flexibility to be brought to the design and component fabrication process and lead times to be significantly reduced. With component production reduced to a matter of weeks, WAAM also offers many benefits for those looking for rapid prototyping. As well as cutting time to market, it allows the creation of high-performance components in a wide range of materials, including aluminium, titanium and steel.
By offering increased design freedom, reduced costs, shortened lead times and sustainability benefits, WAAM is increasingly the DED process of choice from many aerospace manufacturers.
Our expertise in WAAM technology
Find out how WAAM is transforming aerospace manufacturing! Discover the efficiency and cost-saving benefits of Wire Arc Additive Manufacturing (WAAM) for large aerospace components. Get in touch with us today to learn how we can use WAAM technology to revolutionise your aerospace manufacturing process.
[i] McKinsey and the World Economic Forum 2023.
[ii]The buy-to-fly ratio is the ratio of the mass of the starting billet of material to the mass of the final, finished part.