MiniWAAM®
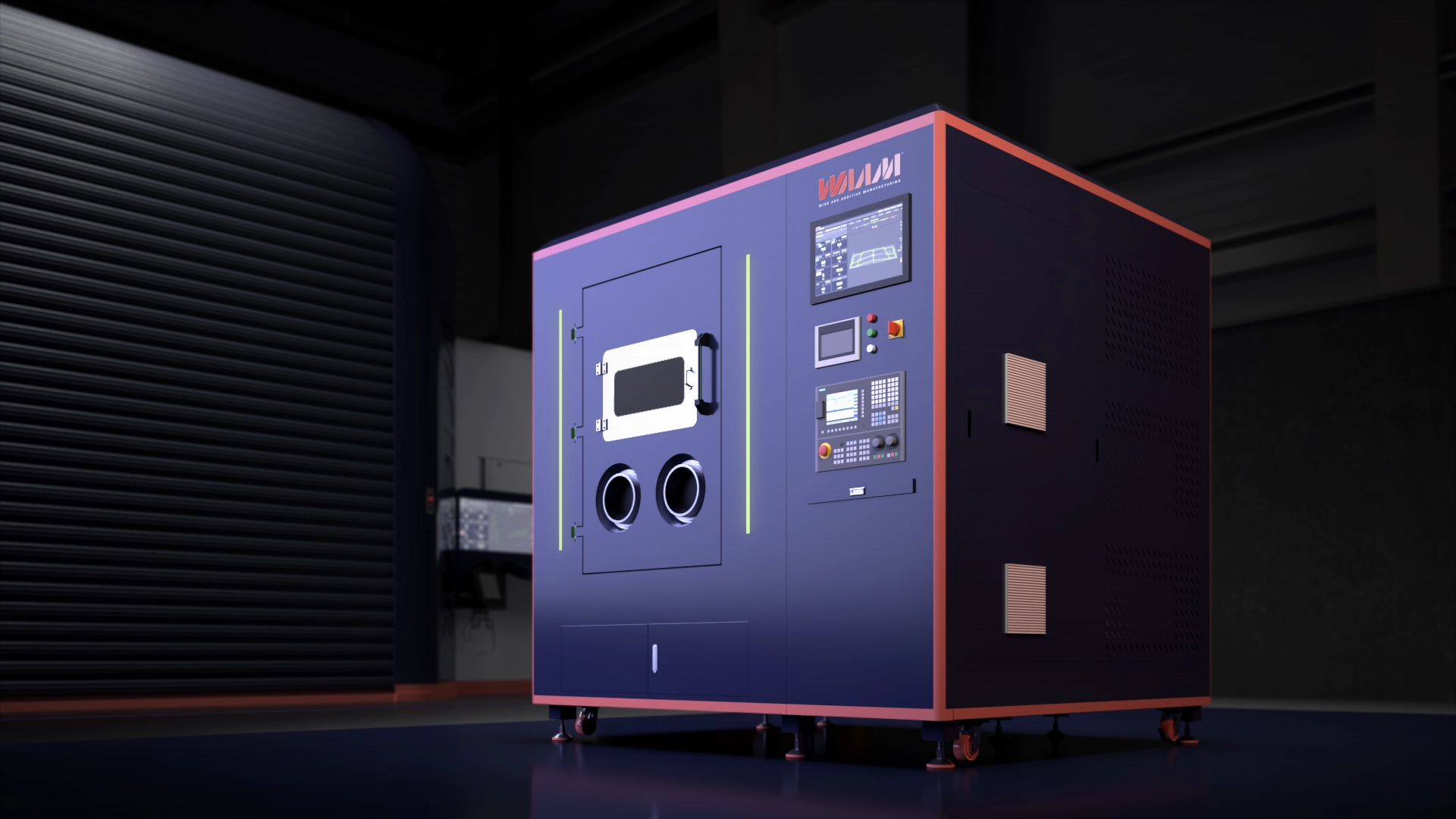
State-of-the-art hardware finally made available to the wider WAAM® community
All of RoboWAAM® intelligence and performance packed in a compact and mobile platform
From prototypes to serial production to R&D, MiniWAAM® delivers economic value across the board
The MiniWAAM® system is designed to seamlessly integrate Wire Arc Additive Manufacturing into your manufacturing workflow – improving productivity, reducing waste, and creating new manufacturing horizons across a broad range of scenarios.
MiniWAAM® BENEFITS
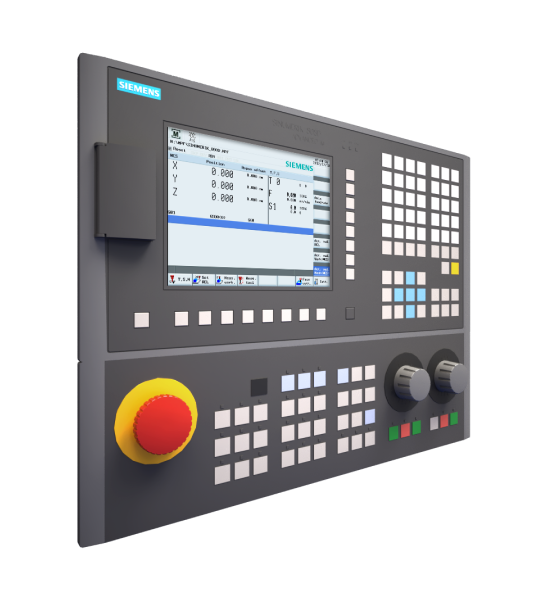
MiniWAAM® SYSTEM
Easy to master
MiniWAAM® comes with our established dual-wire Plasma Transferred Arc process, a Siemens controller, WAAMPlanner and WAAMCtrl.

MiniWAAM® SYSTEM
Innovative
MiniWAAM® ships natively with multi-material capabilities to produce functionally graded components or new alloys in-situ.
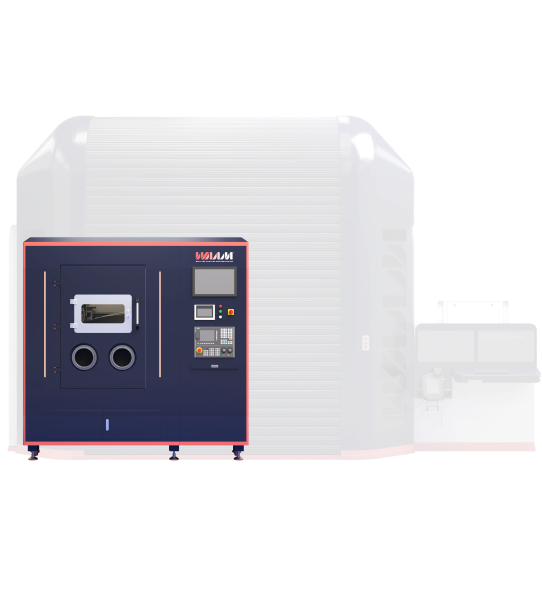
MiniWAAM® SYSTEM
Intelligent
MiniWAAM® packs the same monitoring and control features available on RoboWAAM® Advanced to give you extra confidence in the quality of your parts or the results of your R&D campaigns.
MiniWAAM® SPECIFICATIONS
Technical Specifications
Machine Size
L2400 x W2100 x H2300 mm3
Print envelope
L600 x W600 x H500 mm3
Control System
Siemens PLC
Inner Chamber Size
L1600 x W1500 x H1600 mm3
WAAM Variant
Plasma Transferred Arc
Accuracy
±0.1 mm
Axes
3 cartesian (overhead) + 1 rotational
Materials
Titanium alloys, stainless steel, nickel alloys, and others
Repeatability
±0.1 mm
Rotational table
60kg payload; 500 mm diameter.
Atmosphere Purity
<50 ppm O2
Flatness
±0.5 mm
MiniWAAM® can be deployed to produce prototypes and end-use parts. It is also the perfect companion for process development, metallurgical characterisation, production of mechanical test pieces, exploration of new wires, and testing of new sensors.
WHY MiniWAAM®
This new machine emulates RoboWAAM® Advanced but in a more compact, simpler, and more cost-effective way.
RoboWAAM® has taken the world of large-scale metal additive manufacturing by storm. We have integrated several state-of-the-art technologies for the first time on a large format platform, which has helped many players delivering excellent industrial solutions.
After RoboWAAM®’s success, we’re delighted to introduce its smaller sibling: MiniWAAM®. But watch out – while MiniWAAM® may be smaller than RoboWAAM®, it’s no junior version.
Global Argon Shielding Ensures the Quality of Printed Parts.
Fume Extraction and Filtration Enhance the Workspace Environment.
Internal Chamber Gas Circulation Paired with Active Cooling Facilitates Continuous Deposition.
Comprehensive Process Monitoring and Data Logging.
Cutting-edge dual-wire deposition for increased deposition rates and multi-material printing
Real-time process control to prevent failures.
Premier WAAM technical support.
User-friendly interface and system, suitable for beginners and experts alike.
WAAM3D HARDWARE
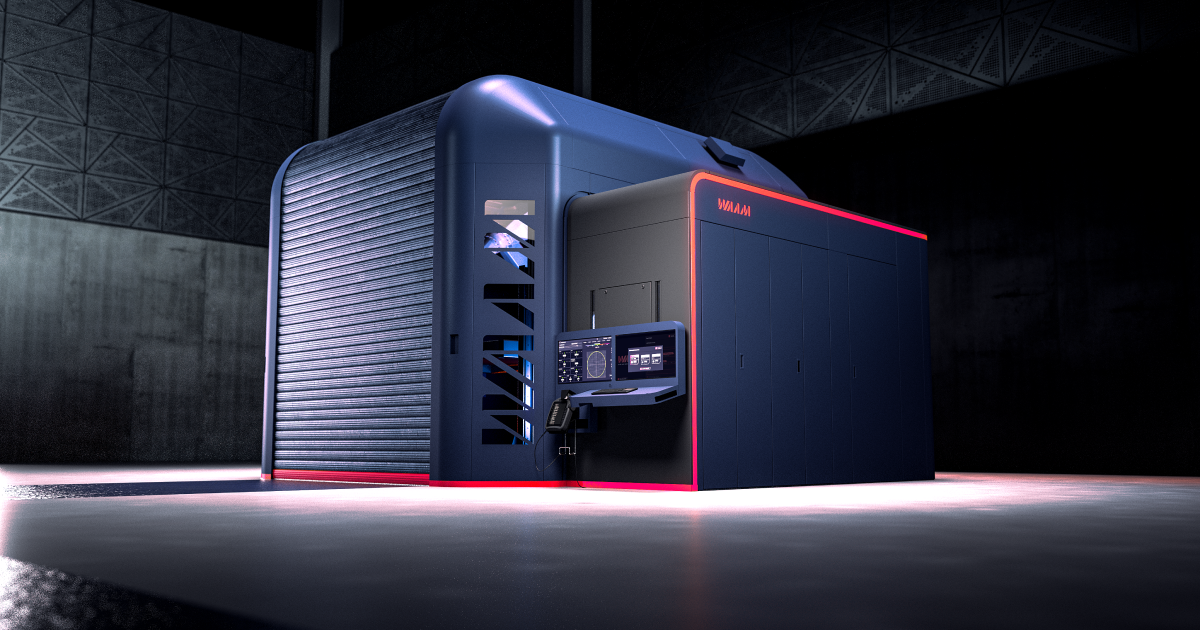
WAAM3D HARDWARE
RoboWAAM® Advanced
The best features of RoboWAAM® Advanced are the ones you do not see: on board fumes treatment, automatic deposition environment purging, quick wire changeover system, and the 40 sensors keeping an eye on the key process variables, tens of times per second.
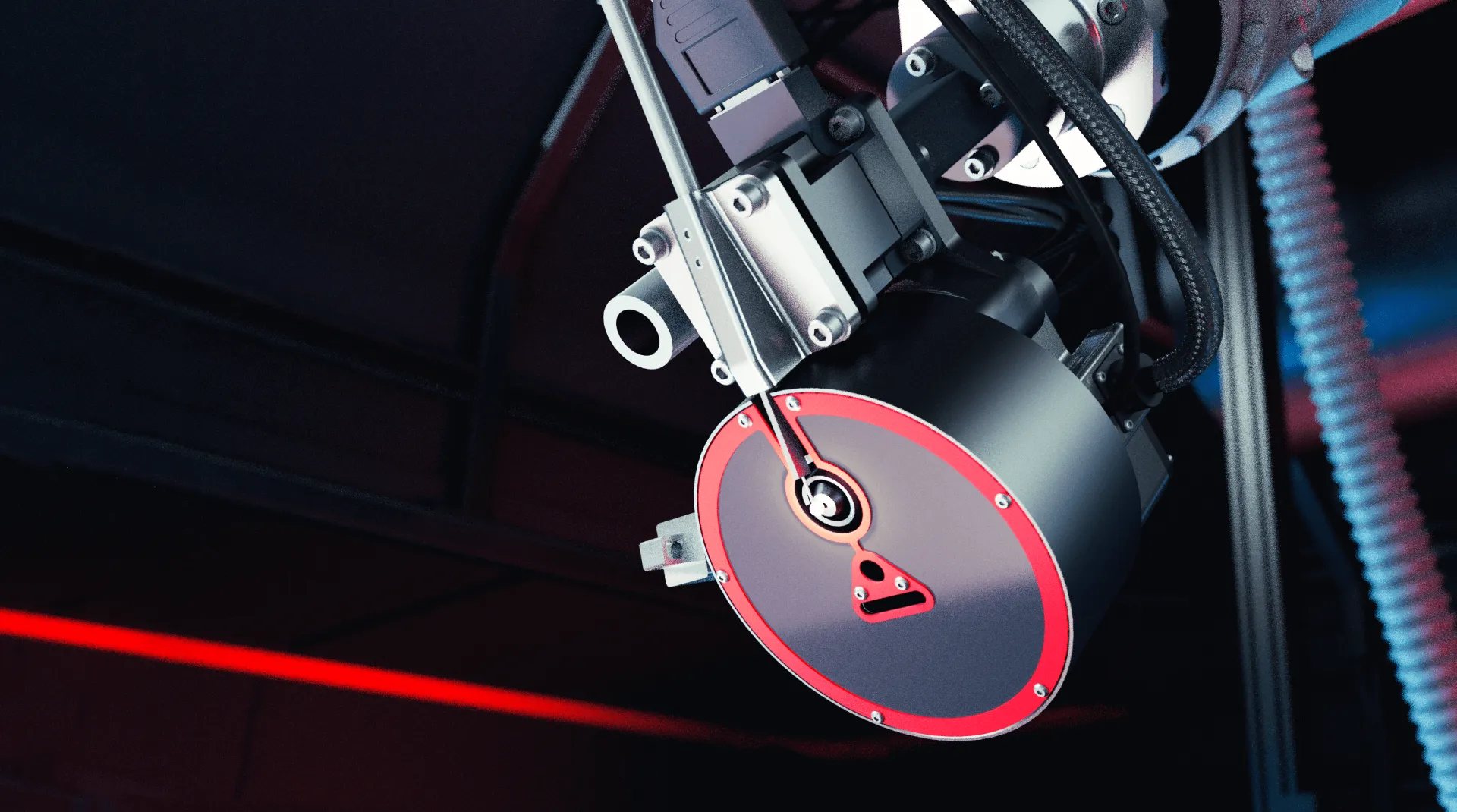
WAAM3D HARDWARE
End Effectors
Much more than a welding torch needs to go at the end of a robot. Our end effectors measure temperatures, provide melt pool imaging, house ShapeTechTM, and with the local-shielding option they also protect reactive materials from oxidation. For PTA options, they also feature automatic positioning of the wire within the plasma arc, to further ensure consistent deposition.