RoboWAAM® XP
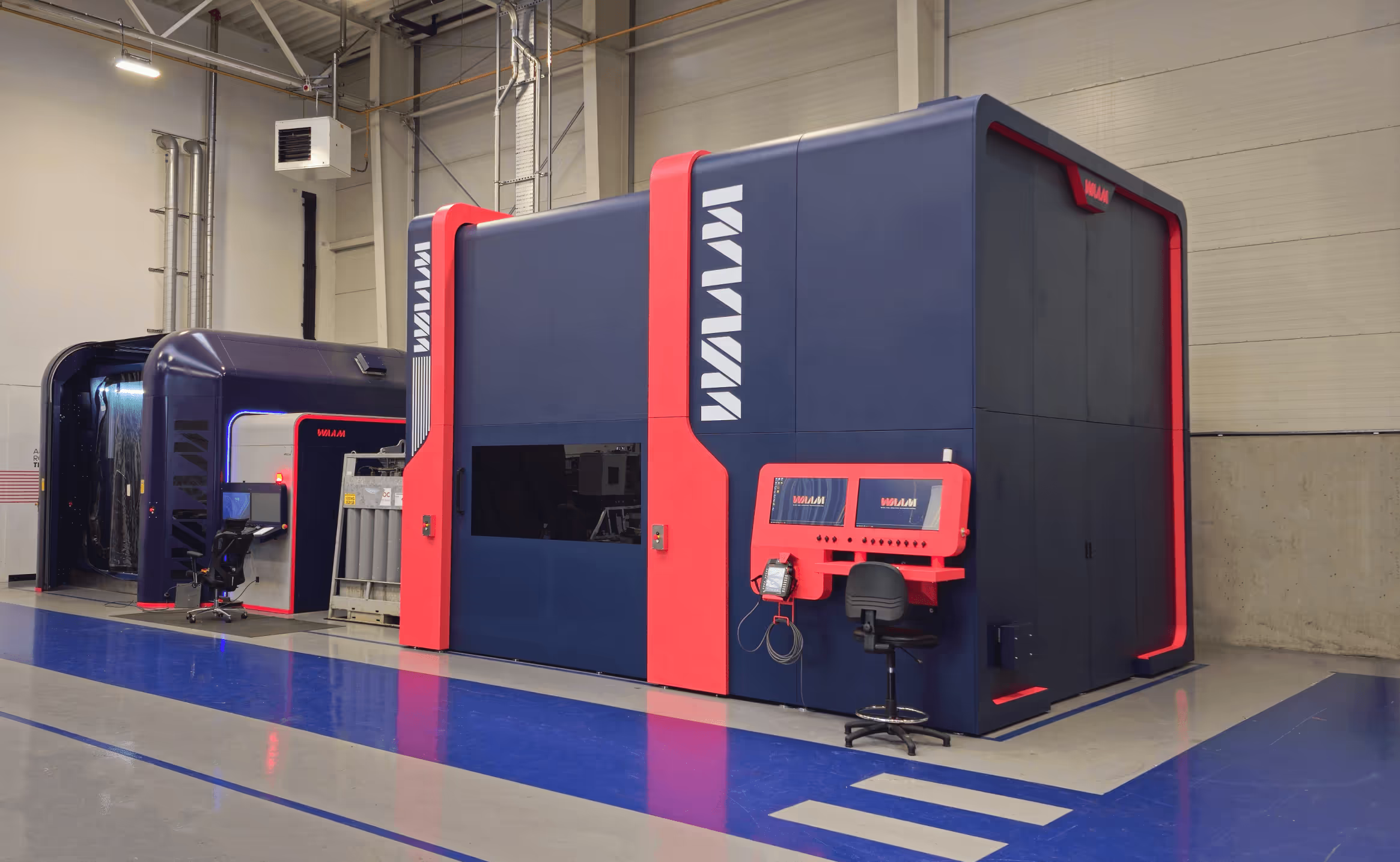
Deposit 100+ kg in less than one day. RoboWAAM® XP features our newest patented CWGMA multi-wire process, which enables industry-leading deposition rates of up to 15 kg/h, as well as MIG, MAG, and CMT.
Build parts of up to 2m x 2m x 2m (configuration dependent) and 2,100 kg. Celebrate WAAM's geometrical capability by using RoboWAAM® XP 8 axes of motion in a coordinated way thanks to WAAMPlanner's automation.
Print alloys of iron, aluminium, nickel, and copper, natively. Join our our partners in the energy, space, marine, and mining industries with whom we've been developing the CWGMA process since 2018.
Our patented CWGMA process not only provides higher levels of control, but also enhances process efficiency with higher deposition rates at the same energy input. We have achieved a significant boost in productivity through 5x process speeds, whilst delivering quality and precision. Printing more than 100 kg in a day is now a reality.
RoboWAAM® XP BENEFITS
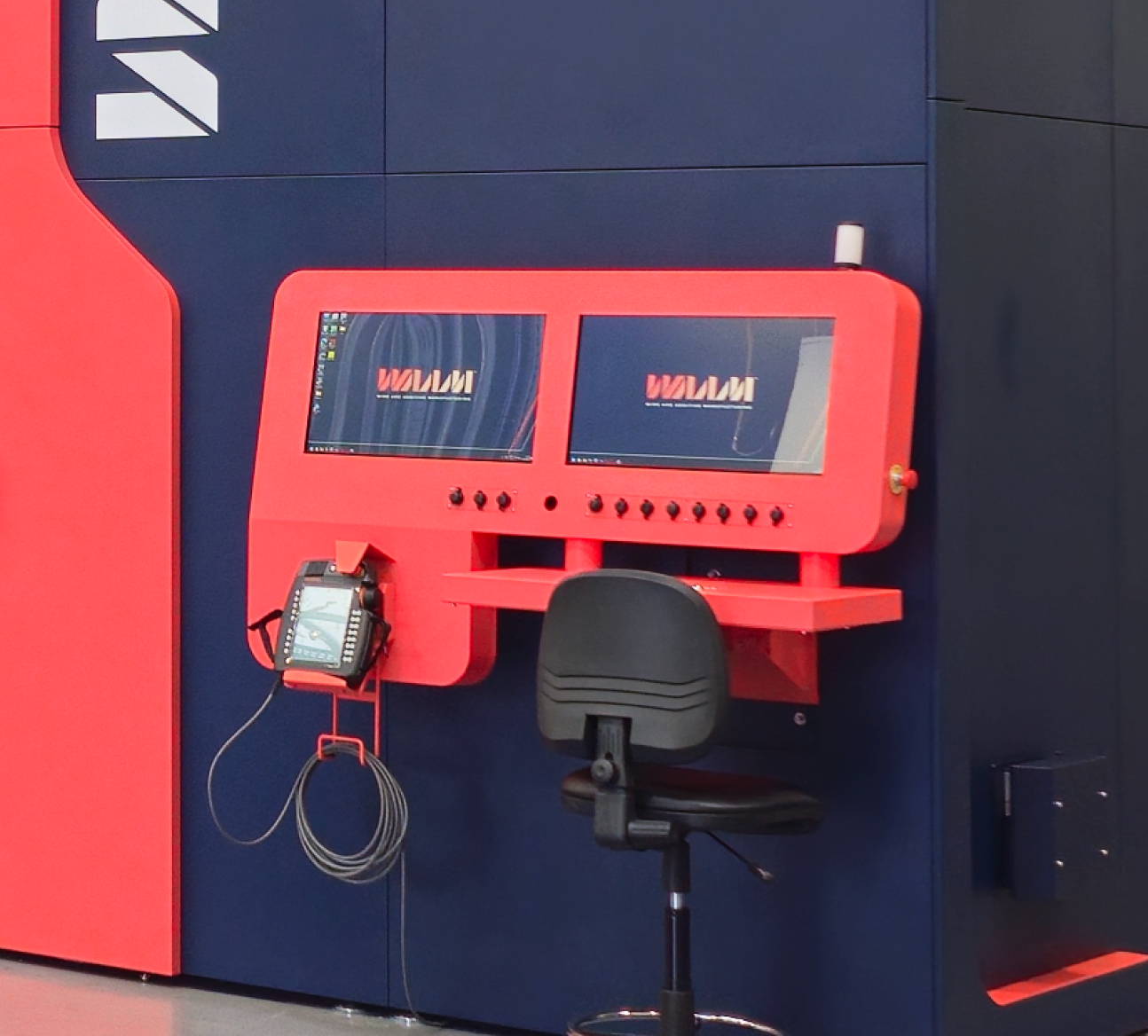
RoboWAAM® XP SYSTEM
Easy to master
RoboWAAM® XP comes with our newest CWGMA process, as well as several established MIG/MAG variants. With its Siemens controller, WAAMPlanner and WAAMCtrl, your user experience will be entirely familiar.
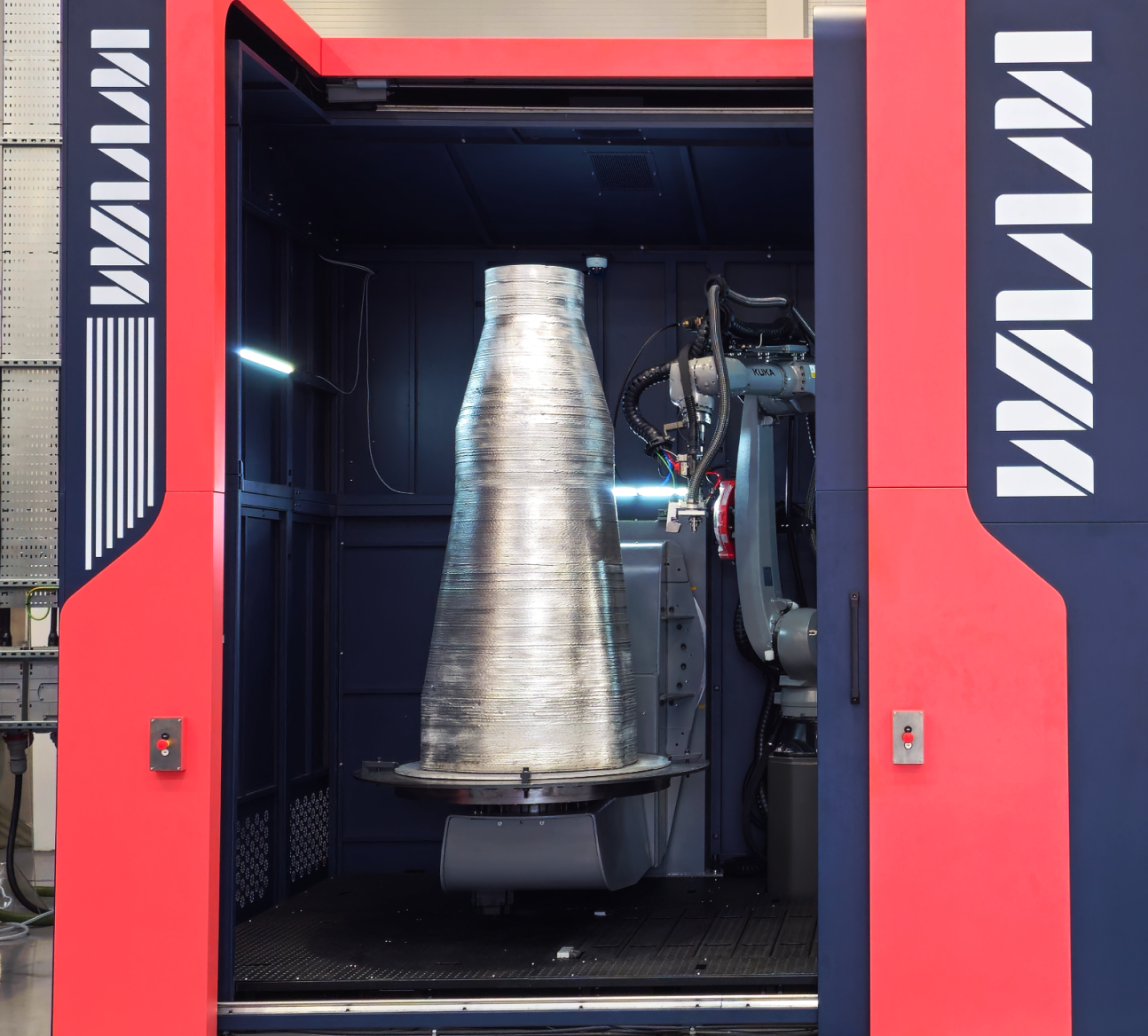
RoboWAAM® XP SYSTEM
Tailored
The addition of the non-energised wire stabilizes the process for a broad range of materials, including steels, nickel alloys, aluminium alloys and others. There are also opportunities to adapt the microstructure to attain the desired properties.
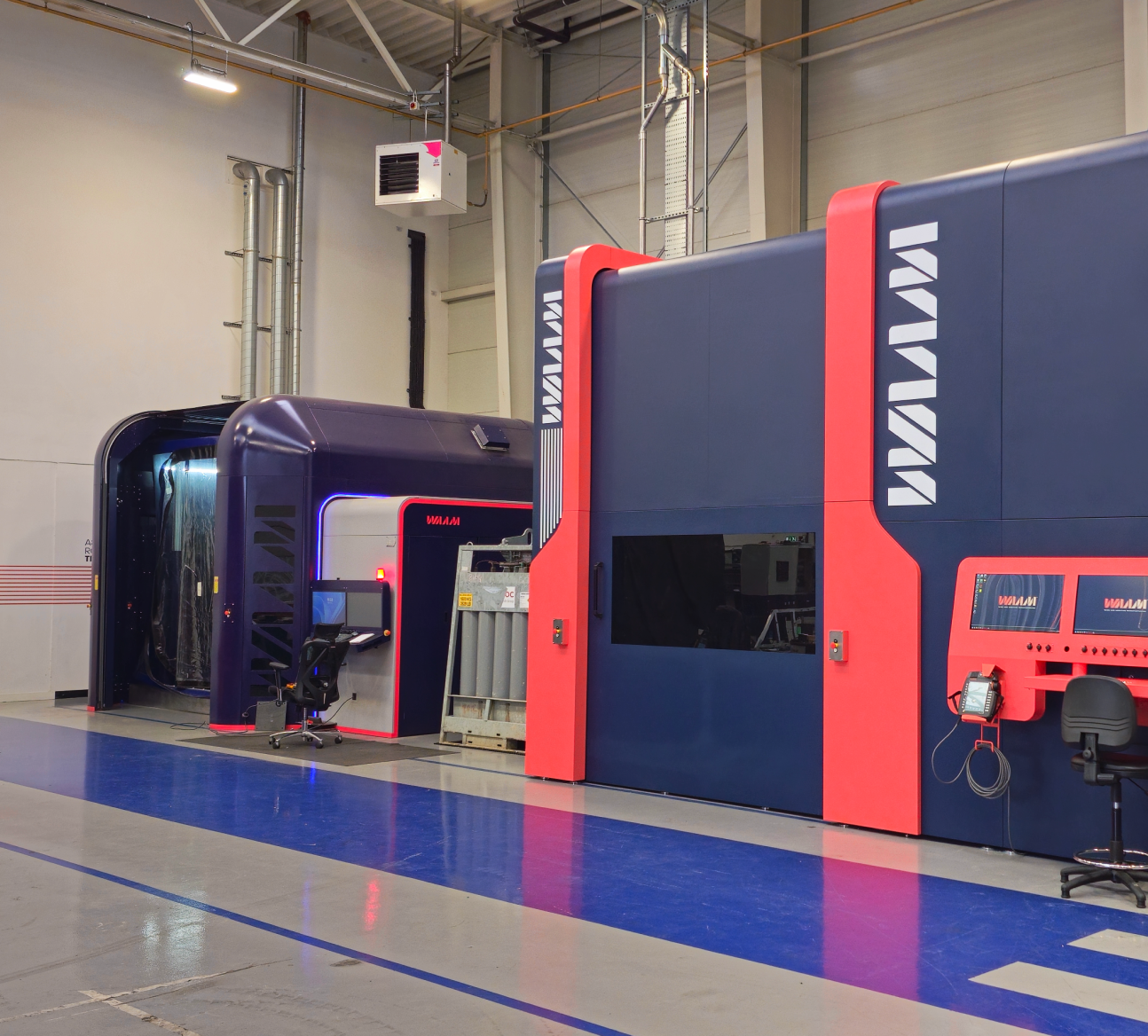
RoboWAAM® XP SYSTEM
Intelligent
RoboWAAM® XP packs the same monitoring and control features available on RoboWAAM® Advanced to give you extra confidence in the quality of your parts or the results of your R&D campaigns.
RoboWAAM® XP SPECIFICATIONS
Technical Specifications
Machine size
5.8m (width) x 5.2m (depth) x 4.3m (height)
Print envelope
2m x 2m x 2m (configuration dependent)
Control system
Siemens PLC
Axes
6 (robotic arm) + 2 (servopositioner)
WAAM® variants
CWGMA, MIG, MAG, CMT
Repeatability
+- 0.05 mm
Robotic architecture
Kuka
Materials
Alloys of iron, aluminium, nickel, copper, and others
Power source and wire feeders
Fronius, Abicor Binzel
Rotationa table (default)
500 kg payload
Rotational table (optional)
2,100 kg payload in continuous rotation
Other optional equipment
Fume management system, pyrometry pack, ShapeTech® for layer height measurement and correction.
RoboWAAM® XP can be deployed to produce heavy metal parts rapidly and consistently. It is ideal for industries with challenging scheduling requirements, either for serial production or spare parts, and even repair of existing assets.
WHY RoboWAAM® XP
RoboWAAM® XP expands the payload and size capability of the RoboWAAM® line without compromising on affordability and quality.
Since its inception, WAAM3D has been dedicated to developing and refining processes that leverage standard off-the-shelf energy sources, including PTA, GMA, and laser. Among these, the PTA process has been a hallmark of WAAM3D, renowned for its exceptional quality and control. This process ensures optimal deposition conditions and superior material properties, making it ideal for applications requiring high precision and quality.
However, the demand for higher productivity, especially in sectors such as energy, has necessitated a shift towards GMA processes like Cold Metal Transfer (CMT) and Pulse Metal Inert Gas (PMIG). While these processes offer greater deposition rates, they fall short in control for Additive Manufacturing (AM) applications due to their linear dependency between material and energy inputs. This inherent limitation restricts their use to simple geometries and applications where precise control of the microstructure and properties is not critical.
Cranfield University's novel, patented CWMIG® process addresses these limitations head-on. This groundbreaking process not only provides a high level of control but also enhances process efficiency by achieving higher deposition rates at the same energy input. The result is a significant boost in productivity through faster process speeds without compromising on the quality and precision required for high-performance materials.
Extra Productivity (XP) for faster speed and increased productivity using patented CWGMA process.
Superior deposition rates of up to 15 kg/h for steel and Inconel alloys,with enhanced process efficiency.
Advanced control of energy input independent to material enables precise optimisation of microstructure and properties for various geometries.
Fume extraction and filtration enhance the workspace environment.
Two wire stock stations capable of 250kg drums each, and torch service station.
User friendly software package with WAAMPlanner for tool path planning and WAAMCtrl for monitoring, ensuring a uniform workflow across all WAAM3D integrated systems.
Premier WAAM3D technical support.
WAAM3D HARDWARE
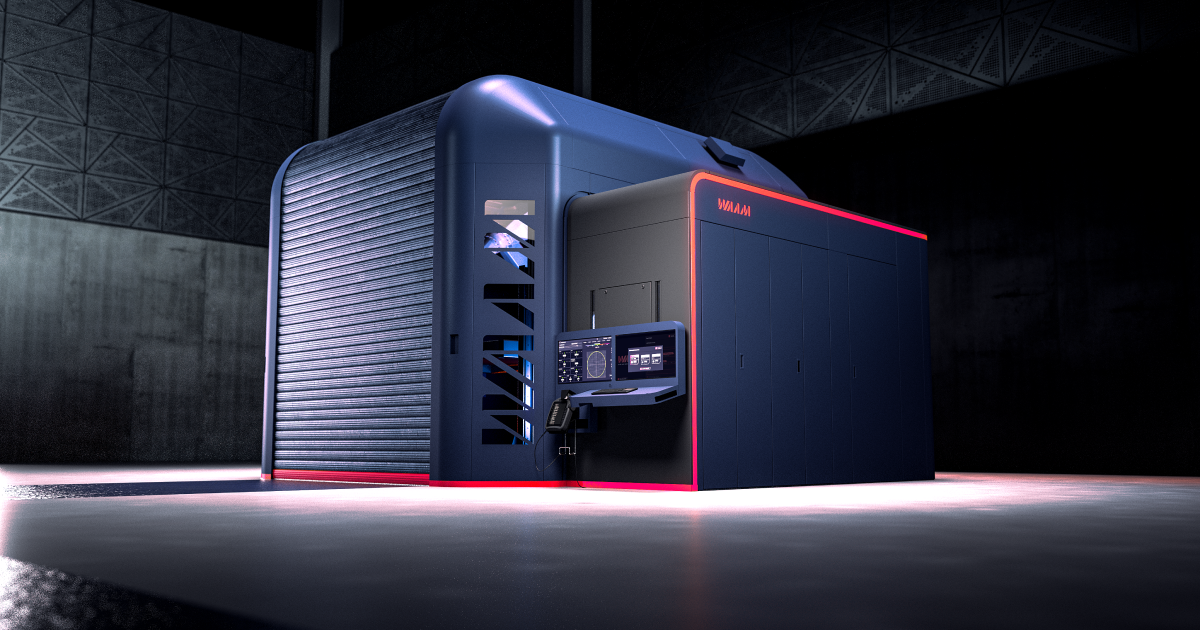
WAAM3D HARDWARE
RoboWAAM® Advanced
The best features of RoboWAAM® Advanced are the ones you do not see: on board fumes treatment, automatic deposition environment purging, quick wire changeover system, and the 40 sensors keeping an eye on the key process variables, tens of times per second.
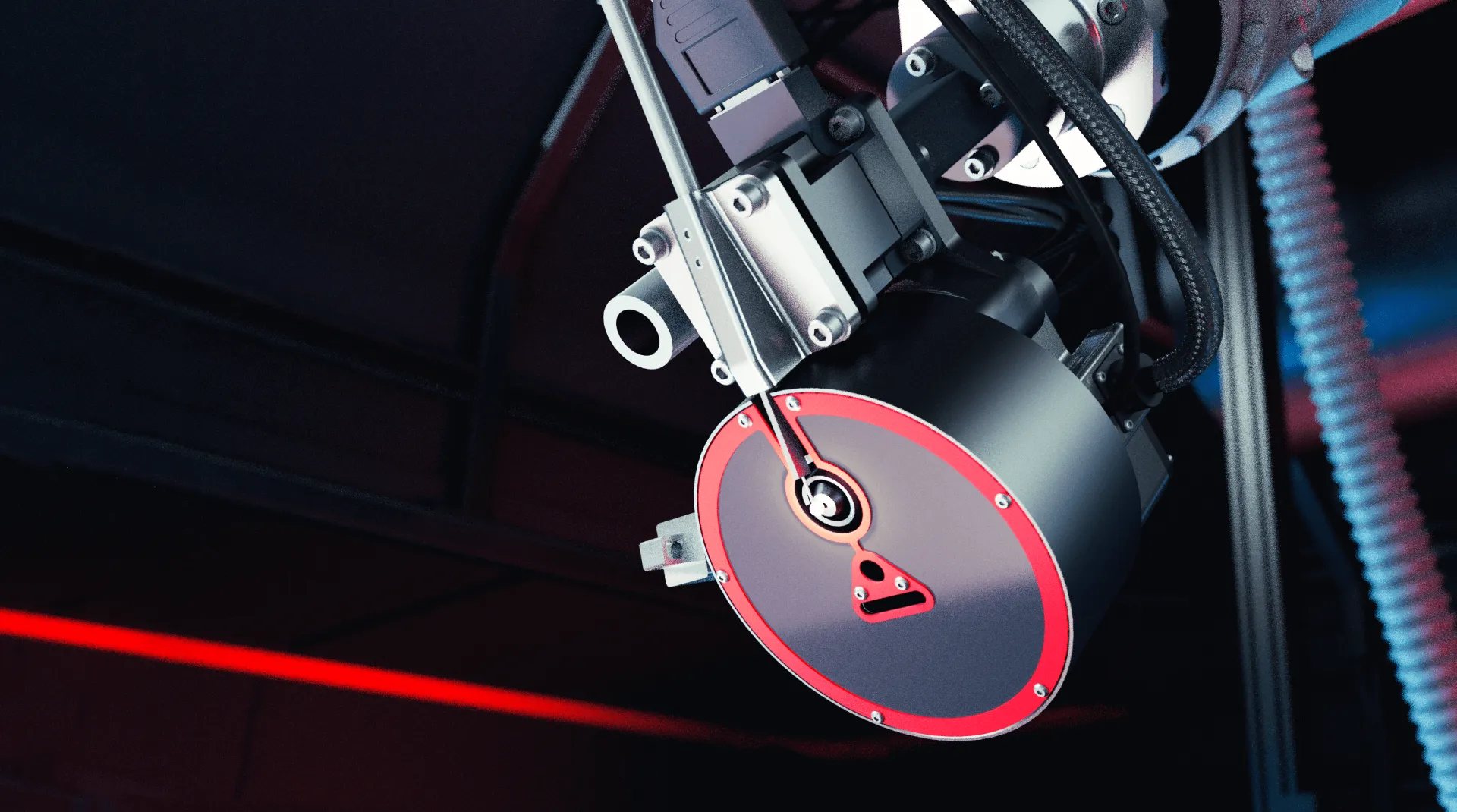
WAAM3D HARDWARE
End Effectors
Much more than a welding torch needs to go at the end of a robot. Our end effectors measure temperatures, provide melt pool imaging, house ShapeTechTM, and with the local-shielding option they also protect reactive materials from oxidation. For PTA options, they also feature automatic positioning of the wire within the plasma arc, to further ensure consistent deposition.