We have developed state-of-the-art WAAM additive manufacturing technologies that help our customers implementing outstanding AM solutions for large-scale industrial metal components.
Wire Arc Additive Manufacturing enables the manufacture of components up to very large size and mass, whether in titanium, steel, bronze, nickel, or aluminium.
Advantages of using WAAM Technology.
With no forging tooling or casting dies, and with reduced material usage, parts are cheaper to produce.
WAAM process creates near net shape components needing minimal finishing, minimising machining swarf and raw material usage.
WAAM can enable onshoring of metal parts and local management of spare parts and repairs.
With our patented in-process cold-work solutions you can achieve forged-like mechanical properties for your parts.
You will get the freedom and flexibility to merge multiple parts into a single part designed specifically for AM.
Your parts can be procured much more quickly leveraging on WAAM’s digital process workflow.
Discover WAAM3D’s family of WAAM dedicated hardware
From sensors to end-effectors and automation to health & safety, we have put you, the user, at the core of our hardware design process. We have redefined what state of the art means, in and around the deposition volume, to give you the best possible experience. What’s more, it all comes together in a vehicle through which we enable you to make the best possible parts: RoboWAAM.
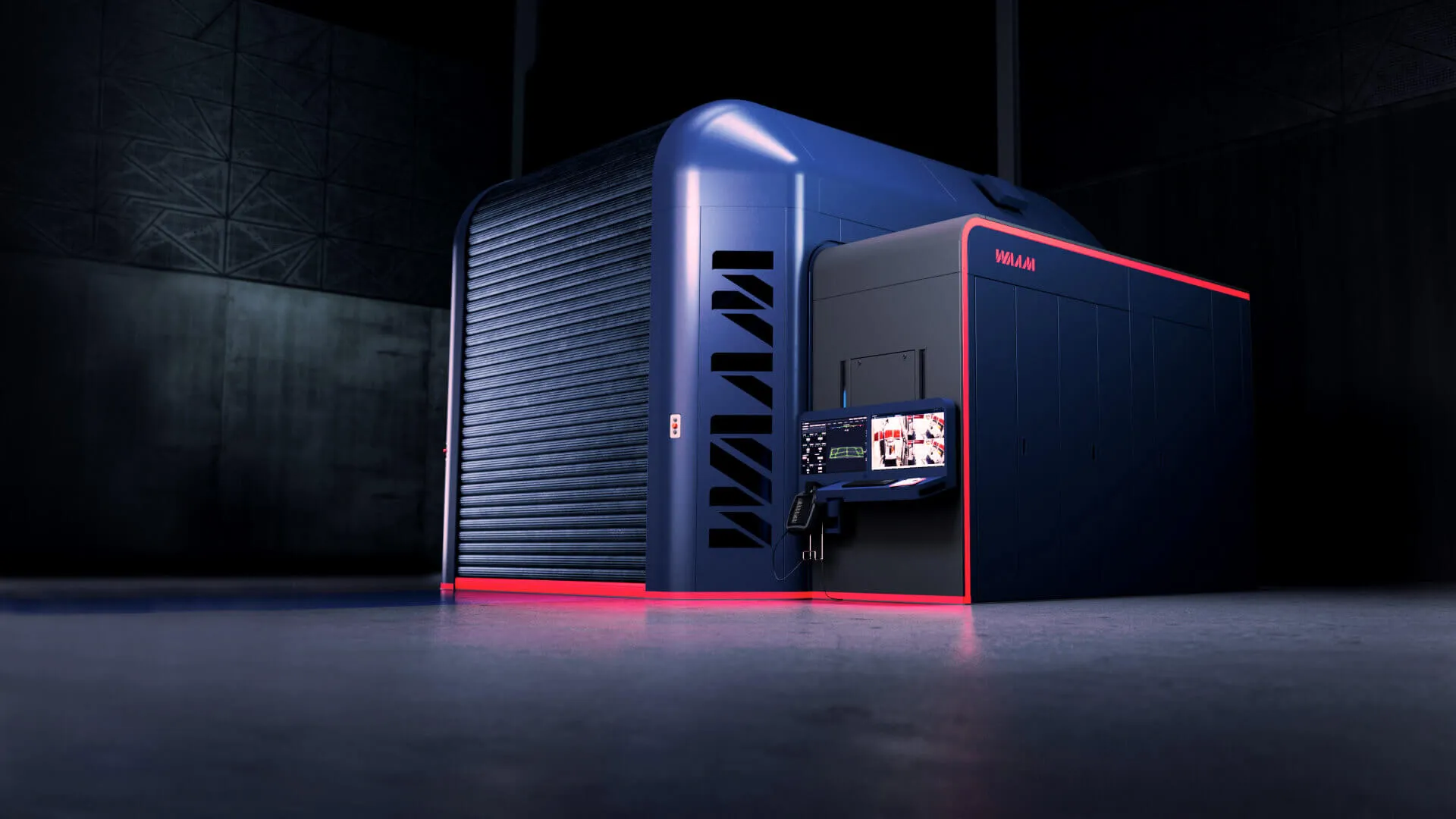
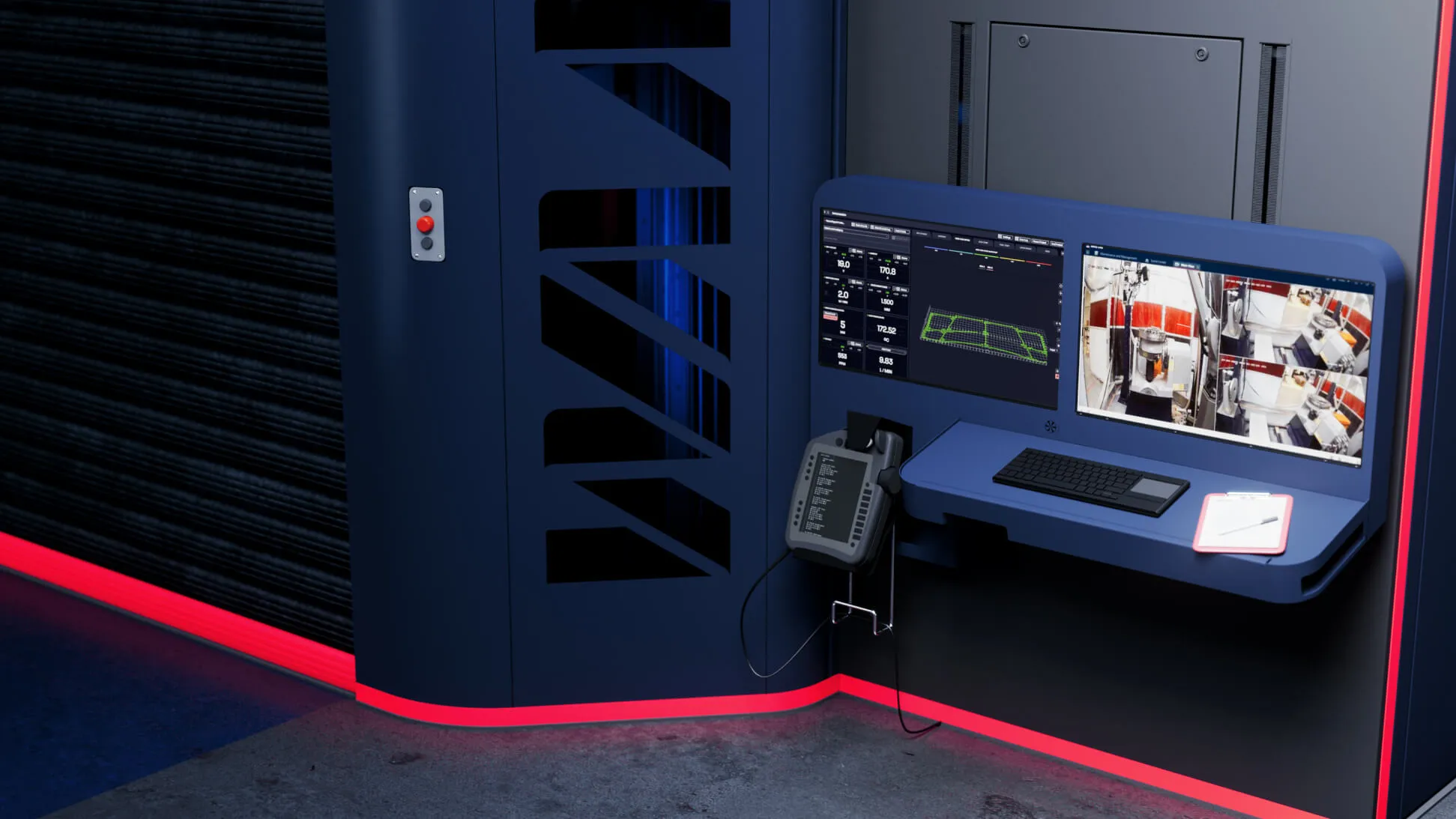
Industries WE SERVE
The latest news and insights from WAAM3D
LATEST NEWS
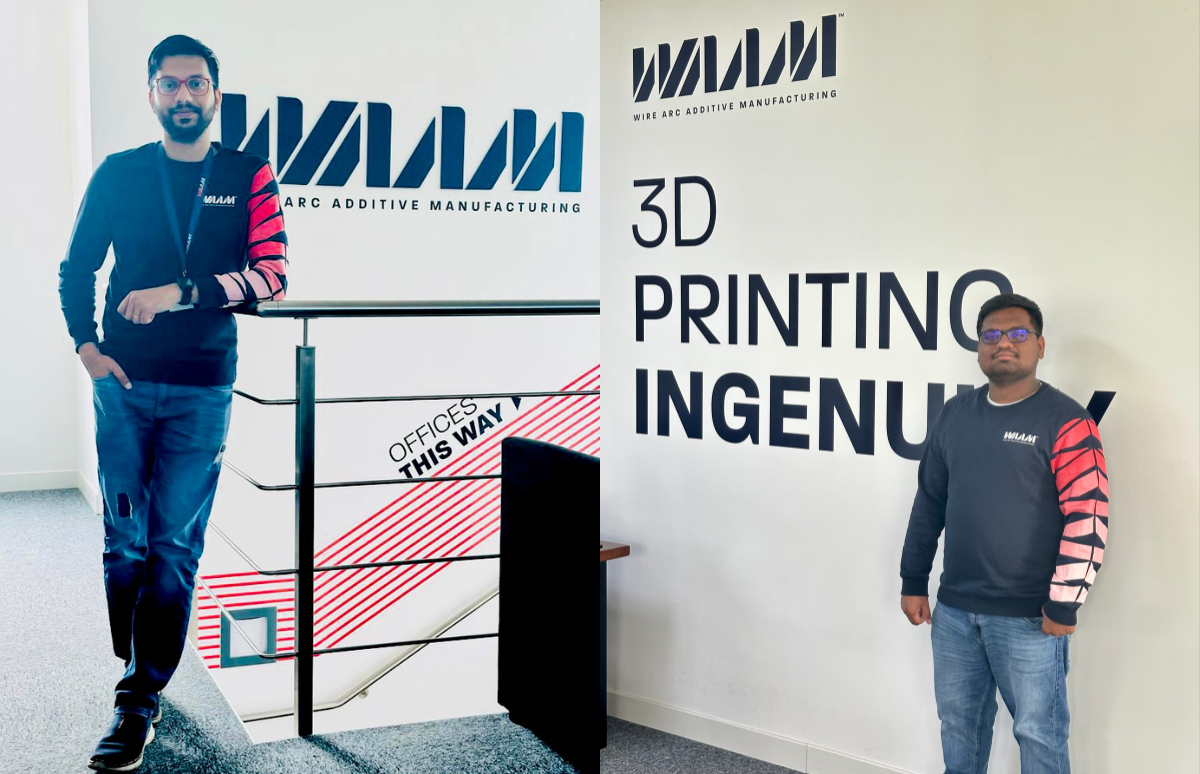
Blog post
July 18, 2023
Cranfield Graduates - Team Spotlight
In this blog, we sat down with some of Cranfield's finest graduates, who now work with us as additive manufacturing engineers. Meet Aravindh Kumaran and Parthiban Raja.
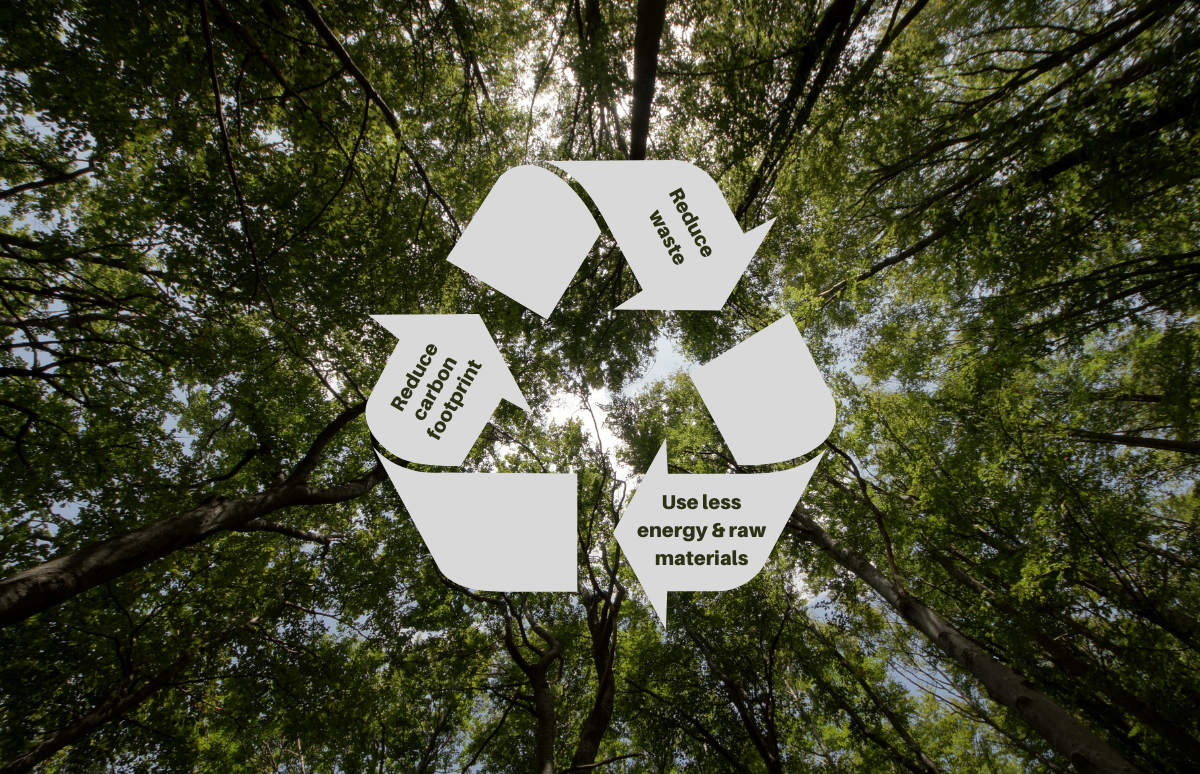
Blog post
June 15, 2023
WAAM – a Sustainable Solution
WAAM can offer manufacturers significant carbon emission and carbon footprint reductions. The WAAM component demonstrated a 40% reduction in environmental impact compared to the demonstration part made using traditional, subtractive fabrication approaches.
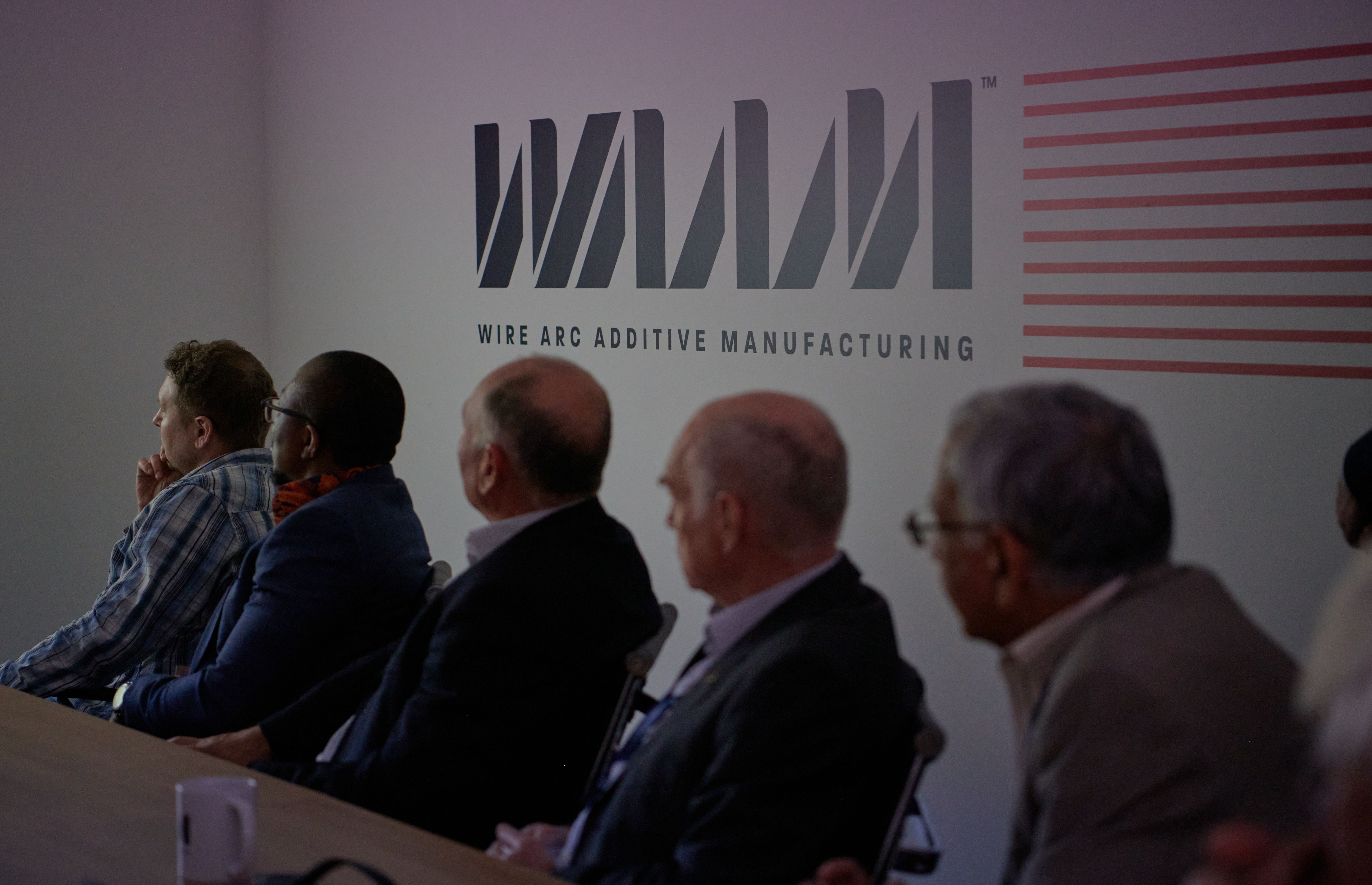
Blog post
April 26, 2023
WAAM – Answering Frequently Asked Questions (FAQs)
Wire Arc Additive Manufacturing(WAAM) is a large-scale 3D printing technology. We answer some of our most frequently asked questions in this blog: What are the advantages of WAAM? Where can the WAAM process be used? And all basic information related to WAAM.