How Wire Arc Additive Manufacturing Benefits Oil and Gas Operators
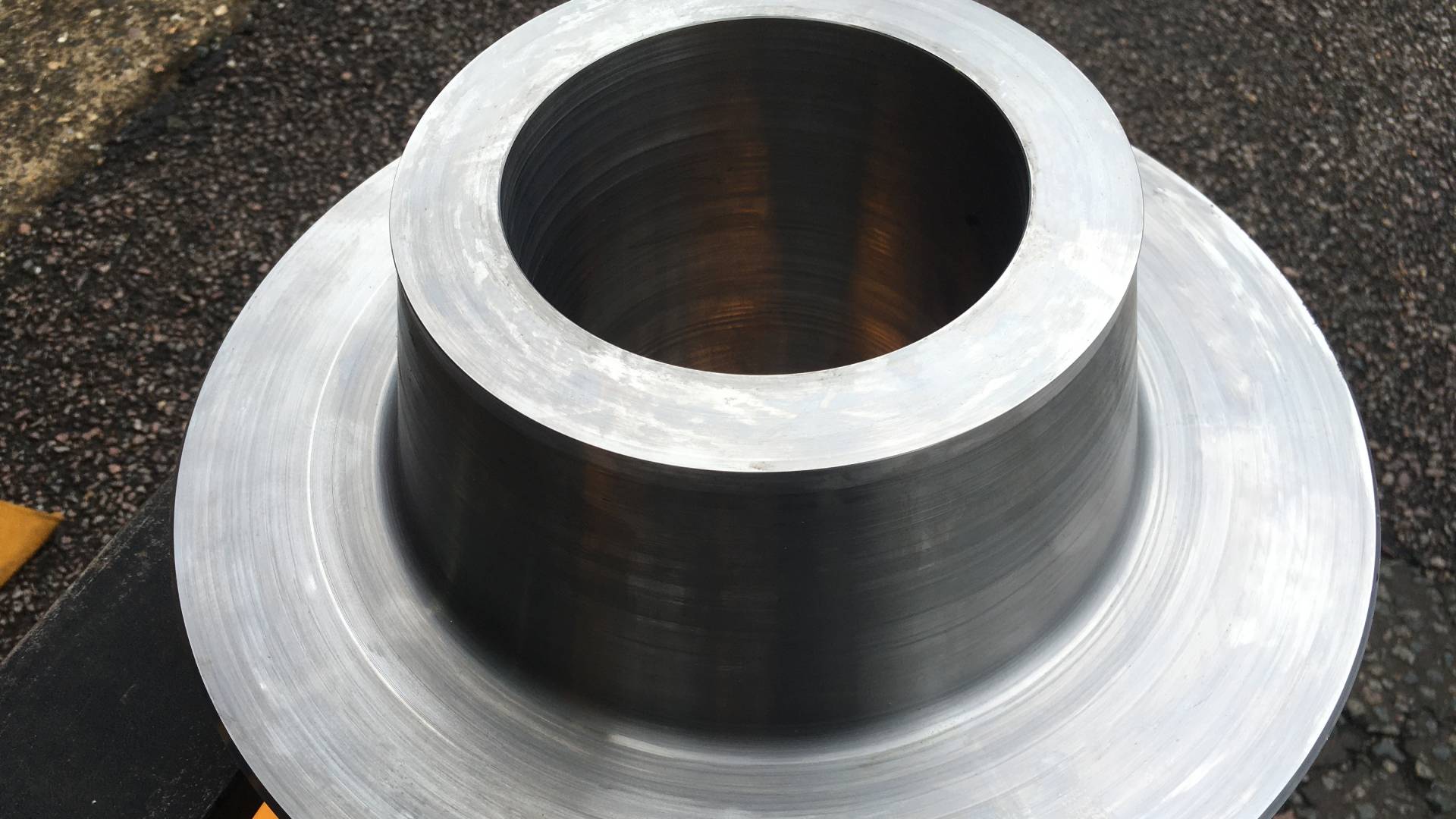
Within this landscape, it might seem strange to talk about additive manufacturing. However, as more and more operators look to save money, whilst promoting more environmental credentials, the manufacturing efficiency of Wire Arc Additive Manufacturing (WAAM®) of medium-to-large scale engineering components is increasing in popularity.
The benefits of WAAM
Cost and lead time reductions
A variety of oil and gas components are already benefitting from WAAM, including mechanical seals, flanges and gas turbine blades. This is because with WAAM it is possible to create large-scale, very near net shape preforms. Importantly, this is done without the need for complex tooling, moulds or dies and can lead to significant cost and lead time reductions for medium-to-large scale engineering components of medium complexity.
- Lead times for large forging scan be up to 14 months (with an additional 4 months for roughing and finishing), WAAM can reduce this process to weeks.
- WAAM enables better material utilisation. For example, a reduction of BTF to <2 leads to cost savings of up to 70% compared to machining the component from solid.
More flexible supply chain
There has been significant pressure on supply chains because of the pandemic, with flexibility reduced across the whole chain. To make component repair and production more sustainable and to build greater flexibility into the supply chain WAAM helps by making manufacturing capabilities more distributed, as well as more cost-effective.
Reduced material waste and environmental benefits
WAAM also delivers a range of environmental benefits to oil and gas operators. The targeted usage of raw material in the WAAM process offers the potential of significantly reducing the carbon footprint of manufactured large and medium scale components.
- The WAAM process minimises waste, and material-usage is very high at approximately up to 98%[i].
- WAAM-based manufacturing also delivers significant energy and CO2 emission savings.
- WAAM has long been used to repair structures, extending the life of components, and delivering even greater environmental and cost benefits.
Reduction of inventory and logistics costs
An additional benefit of WAAM is that it can enable the reduction of inventory and logistics costs by focusing on local, on-demand manufacture. Helping companies to resolve spare part production and repair issues, quickly and as cost-effectively as possible.
As can be seen, WAAM offers a range of benefits to oil and gas operators. For more information on how WAAM can benefit you, contact us here.
[i] Paolo C. Priarone, Emanuele Pagone, Filomeno Martina, Angioletta R. Catalano, Luca Settineri, Multi-criteria environmental and economic impact assessment of wire arc additive manufacturing, CIRP Annals, Volume 69, Issue 1, 2020, Pages 37-40,