The RoboWAAM System as the Tool of Choice for R&D
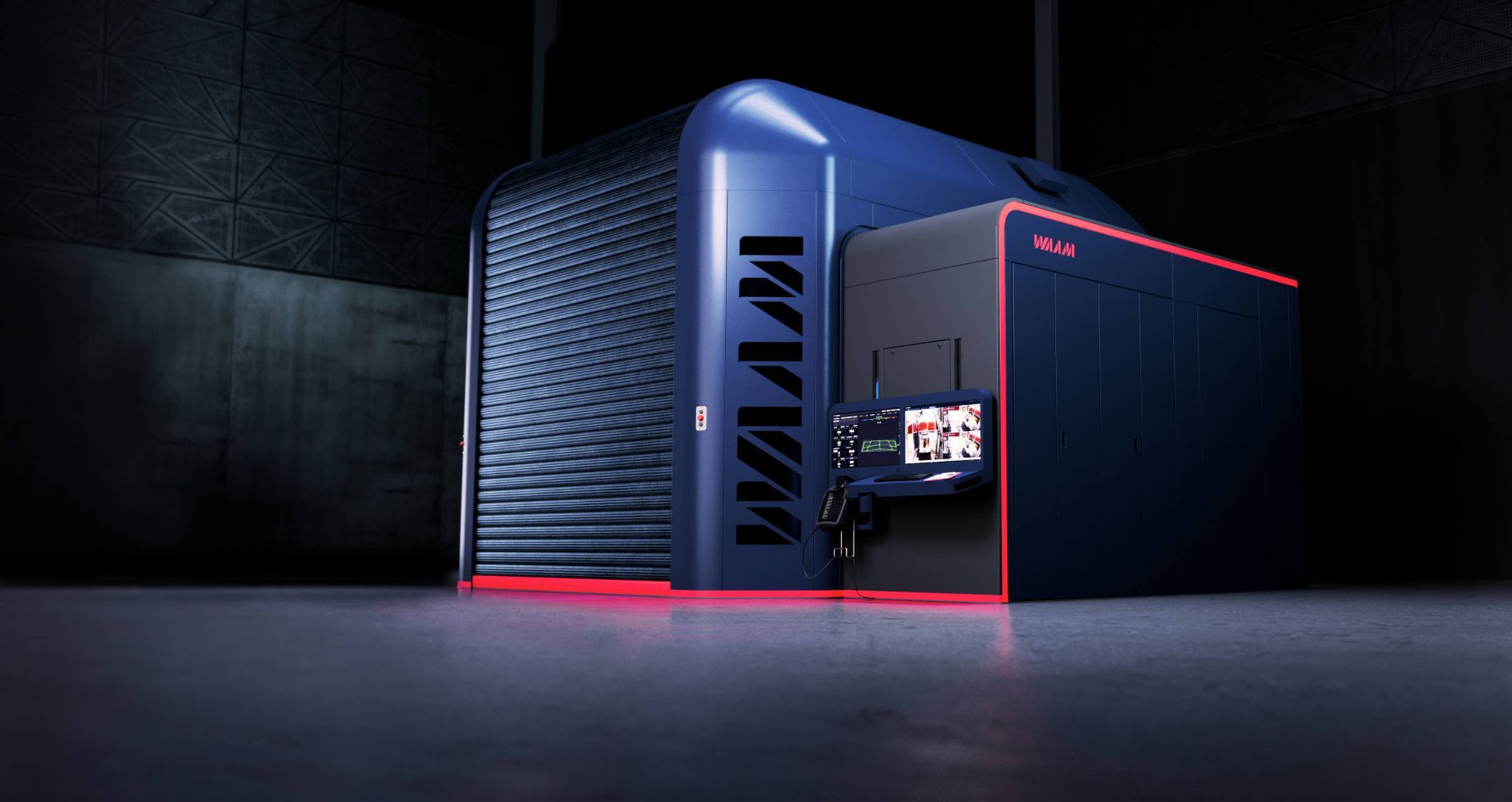
It has often been quoted that "a man is only as good as his tools", and anyone who has tried to cut with blunt scissors will most likely agree! When it comes to the 3D printing of large-scale components however, the appropriateness of the tool takes on a whole new level of importance.
A relatively recent addition to the component production toolkit is Wire Arc Additive Manufacturing (WAAM®) technology. As well as being highly effective in delivering large format 3D printed components for sectors as diverse as aerospace, marine, energy, and construction, the R&D capabilities of WAAM machines are considerable:
Reconfiguration capability of WAAM3D machines
WAAM3D’s RoboWAAM is a 3D metal additive manufacturing machine engineered and built for WAAM in the UK. Powered by the operating system WAAMCtrl, it has novel sensors, specialised end-effectors and advanced health and safety solutions. A result of two decades of R&D work born out of academic research at Cranfield University, RoboWAAM is an integrated system that, thanks to its reconfigurable build envelope, has the flexibility to accommodate a variety of part geometries (e.g., frame structures as well as rotational components). RoboWAAM features the highest payload, largest build volume and the most on-board sensors of all the wire-DED systems out there.
Testing new materials and new parameters
In theory, there is no limit to the types of material that can be tested and printed using WAAM, particularly using the Plasma Transferred Arc (PTA) process. The PTA process is generally used to deposit most of the weldable alloys, such as alloys of titanium, aluminium, iron, nickel and many more. For some of these alloys, automatic process parameter calculations are available, however users can create their own process parameters if they want to see what is possible with both new and existing alloys.
Monitoring capabilities with WAAM3D
With any R&D activity, it is key to keep track of as many variables as possible, be they temperature fluctuations, voltage and gas flow, or geometry to name but a few. With RoboWAAM, all of this work is done automatically. The process monitoring software and control and data analysis is informed via the 20 sensors keeping an eye on the key process variables automatically, tens of times per second, eradicating the need to integrate external monitoring systems into the process.
Thanks to the many years invested in developing the WAAM3D Ecosystem of technology, software, hardware and feedstock, it is now possible for the full potential of 3D metal additive manufacturing to be explored.
If you'd like to find out more, please contact us here