WAAMCtrl and What it Does
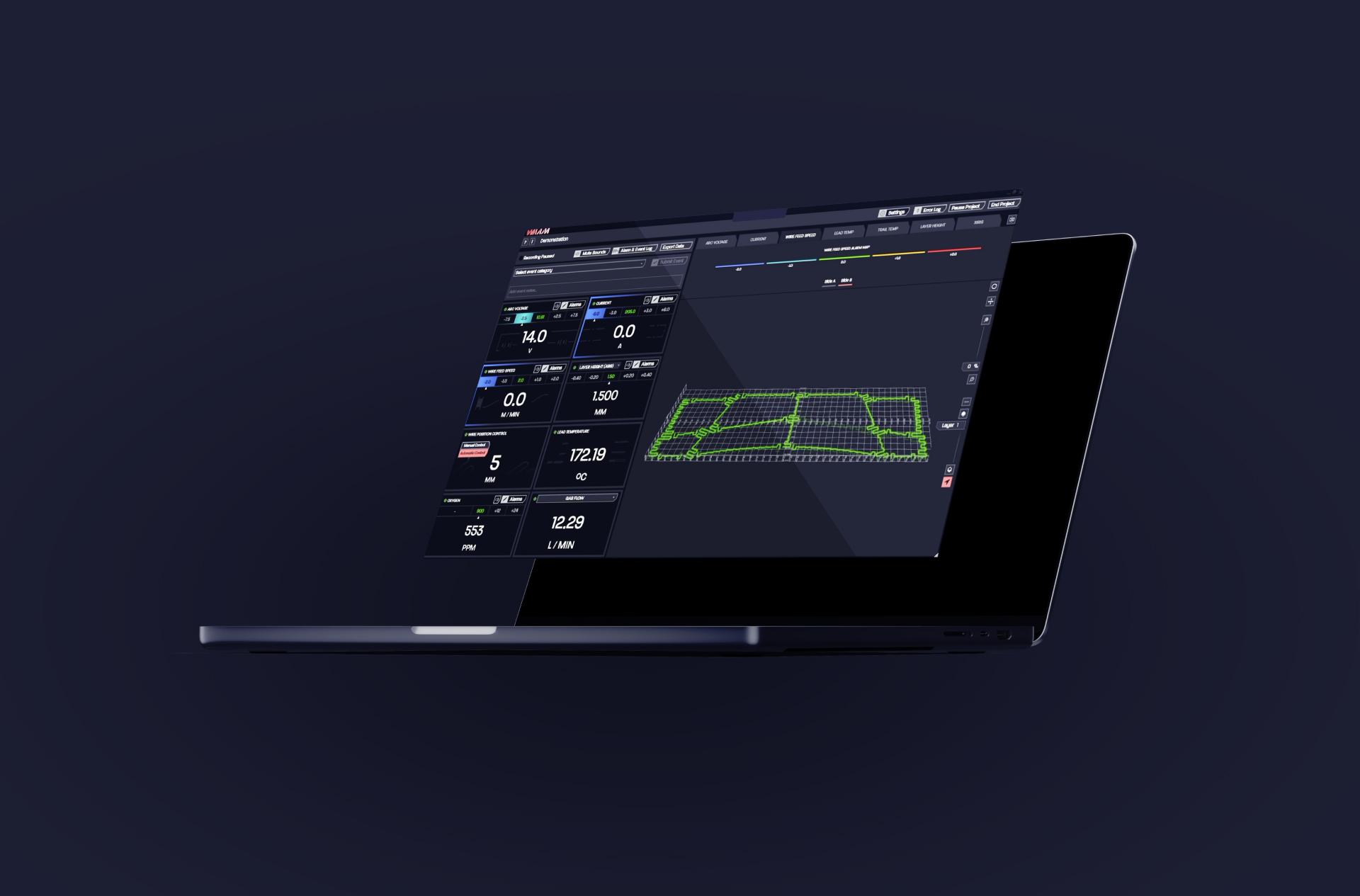
Key to the success of any component is that it meets set parameters and is safe. Wire-arc additive manufacturing (WAAM) can deliver many benefits to manufacturers, yet in the past the qualification and production aspects of the process were more difficult to monitor. Now, thanks to the introduction of WAAM3D’s WAAMCtrl®, a digital quality control tool with the support of robust Statistical Process Control (SPC) is now possible.
The benefits of Statistical Process Control in WAAM
SPC is a scientific data-driven technique that is used to ensure consistent performance, to a stated design, in the production process. By employing SPC when WAAM components are being created:
- Overall product quality is controlled
- Any variations are eliminated if repeat parts are needed
- Compliance with regulatory and customer requirements is provable
With uniformity so important when it comes to producing components, SPC enables the detection and correction of any potential errors before they can cause any major problems to the production process. However, in the past, it was difficult to apply SPC to WAAM, due to the many dependent and independent variables included in the process. Thanks to innovative product development by WAAM3D and a novel underpinning hardware infrastructure, SPC is now possible when undertaking WAAM.
WAAMCtrl delivers ultimate process control
WAAMCtrl is an all-encompassing operating system for WAAM3D’s RoboWAAM®, which is a next generation large format 3D metal additive printing platform for multi-metre metallic part development for aerospace, defence, oil and gas and research communities.
WAAMCtrl enables the monitoring, control, digital twin mapping, hardware and health and safety management of a component, as it is being produced. As well as enabling operators to have a fully controllable production process, WAAMCtrl also produces fully auditable data storage, quality logs, and interactive data navigation to enable the demonstration of compliance in a fully repeatable way.
WAAMCtrl’s primary features
- Process monitoring of voltage, current, wire feed speed, travel speed, wire position, layer height, pre- and post- deposition temperature, oxygen, gas flow and melt pool in combination with RoboWAAM’s hardware
- Database logging
- Real time rendering of 3D map of logged data
- Industry 4.0 enabled with downstream big data analysis
- Can be integrated with ERP systems for push to post-processes
- Seamlessly integrated ontoWAAM3D’s hardware and sensors
Real-time control
Tens of times per second, state-of-the-art sensors transmit information to WAAMCtrl for monitoring and control, enabling the operators to see in real-time how the project is progressing. Real-time colour-coding of the 3D charts help those producing the component to make sense of the big data, mapped over the part’s geometry.
Evaluation
Audit Exporting enables the easy monitoring of the component’s progress, managing the production of the part from material source to shipping. Also, the progress and quality of a component can be evaluated from anywhere in the world, with templated Audit Forms. WAAMCtrl records all the process data, making them easily accessible should the production process need to be assessed. Thanks to WAAMCtrl’s use of SPC, its monitoring output enables the demonstration of robustness, validity and compliance to certification boards and other regulatory bodies.
For more information on bringing uniformity into yourWAAM processes visit waam3d.com/contact